Battery recycling technologies
The production of lithium-ion batteries is a growing market. But the more lithium-ion batteries are produced, the more batteries will have to be recycled. Battery manufacturers are dealing with two different types of recycling:
- recycling of production scrap during the manufacturing process
- end-of-life (EOL) recycling of batteries that are no longer used.
It is estimated that in the EU alone, there will be around 325.000 tons of available battery scrap in 2030. Among this scrap, there are valuable and critical raw materials like manganese, cobalt, lithium compounds or graphite. These can now be reintroduced into the production cycle, thus making the production of lithium-ion batteries much more efficient.
The quantity and quality of the recovered material depends on the choice of lithium battery recycling technology. With ON's battery recycling solutions, you can be sure that you lose very little valuable material, making your battery production process as efficient as possible. For this purpose, ON provides you with various lithium battery recycling machines and systems, developed and configured for your specific requirements.
Hosokawa Micron offers innovative solutions for direct recycling of production scrap during the battery production process. Here, our system takes the production scrap, cuts the foil into small pieces and delaminates the cathode or anode material to send it directly back to the coating process.
Direct scrap recycling of lithium-ion batteries
During the production process of lithium-ion batteries, there is a lot of production waste. This occurs mainly during the coating process, for example, when sorting out defects such as pinholes, inclusions and other coating faults, due to edge trimming or rejects during the finishing process. In total, about 10% (or considerably more depending on the process) of the coated cathode or anode foils end up as rejects and have to be recycled. This is a problem when it concerns the valuable active materials, i.e. the NMC or LFP of the cathode foils or the graphite-silicon mixtures of the anode foils.
Currently, this foil scrap is collected from battery manufacturers by 3rd party recycling companies. ON has developed a new process for direct scrap recycling of production scrap where the scrap can be recycled at the production site and fed directly back into the production cycle. This makes production more efficient, and the cathode and anode material scrap can be almost completely recycled without impurities and be reintroduced into the coating process. Customers also save themselves the effort involved in external recycling.
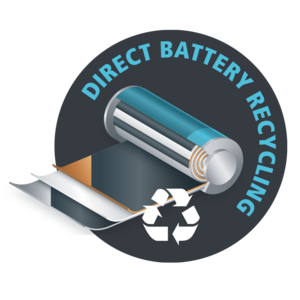
Direct recycling of the active materials
ON’s process of direct recycling during the electrode production: one process can be applied to both anode or cathode material. However, separate production lines are necessary to recycle anode and cathode material.

The direct inhouse recycling process of the electrode scrap consists of two steps: cutting and delamination.
1. Cutting: To prepare for the delamination process, the Rotoplex cutting mill is the machine of choice. It has to be operated with inert gas both for safety reasons and to protect the material. The material can be fed directly via a feed chute. Alternatively, batch feeding of the collected scrap (e.g. in barrels) is possible. The Rotoplex is available in different sizes and can achieve throughputs up to approximately 3,800 kg/h. The cross-scissor-cut rotor developed by Hosokawa Alpine and proven over many years also ensures a very low energy input into the material and makes the production scrap recycling very efficient.
2. Delamination: The next process step is delamination of the cut electrode foil. Electrode material and carrier foil are prepared for separation. The adhering active material is removed from the carrier foil.
The quality of the battery recycling process and the recovered material depends on the clean shredding and cutting of the carrier foil.
Test centre for battery recycling solutions
To find the best battery recycling technology for you, we will be happy to carry out trials with your electrode foils in our test centres. Together with you, we validate your process with tests. This includes tests or general feasibility as well as scale-up trials. So you can be sure to obtain lithium battery recycling machines that best suit your product and your requirements.
From the first quarter of 2025, a special test centre will be available to you for trials on direct scrap recycling during ongoing battery production. We will test how our process fits into your production process and how you can make your battery production more efficient and at the same time fulfil the prescribed recycling quotas. We carry out trials with your materials on Hosokawa Alpine machines to find the optimum solution for you - naturally with the highest safety standards for your and our employees.
Would you like to know more? Then get in touch with us!
Direct scrap recycling of the cathode foil materials
In the recycling of cathode foil materials such as NMC or LFP there is additional point to consider: Due to the formation of toxic carcinogenic substances during processing, inert processing and containment solutions are necessary for the recycling of the cathode materials. Additionally, the equipment for this process has to be wear-protected. Validation of this process is carried out in the test centre.
End-of-life: Battery Black Mass recycling
When a battery reaches the end of its life, the raw materials it contains can be recycled. This end-of-life recycling is an environmentally sustainable and economically viable battery recycling technology, as it reduces the need for new raw materials.
After collection, the battery is dismantled, shredded and processed to produce the “black mass”. The black mass of the anode contains high amounts of graphite, whereas the black mass of the cathode consists of lithium, manganese, cobalt and nickel. End-of-life recycling extracts these valuable materials from the black mass so they can be re-used in the production of new batteries.
ON provides systems for EOL battery recycling plants to delaminate the aluminium or copper foils, i.e. to detach the cathode or anode material from the supporting film. The mill of choice for black mass battery recycling is the UPZ fine impact mill which is available in various sizes and with various types of grinding elements. It separates the black mass from the foils and prepares the material for sifting and classification. Due to the toxicity of the material, ON provides specific containment solutions.
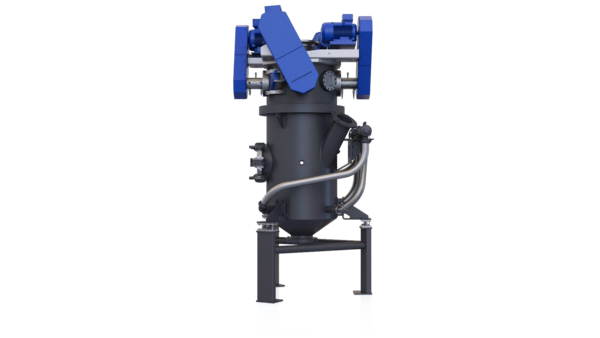
Machines for battery recycling
Whether you are interested in black mass recycling or direct recycling of lithium-ion batteries, ON can provide you with the right machines and systems for your specific process. Get in touch with us and find out how you can benefit from our battery recycling solutions!
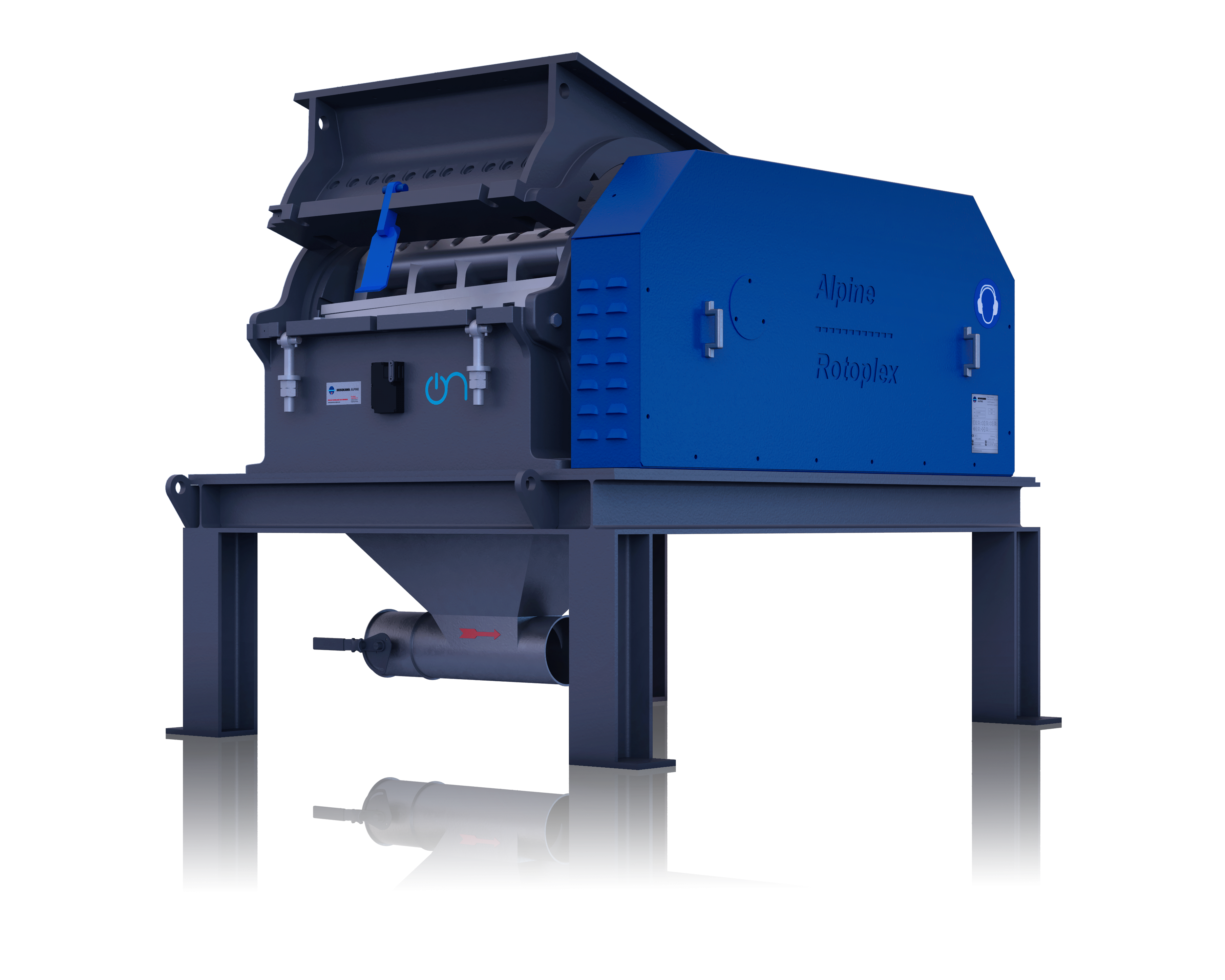
Rotoplex Cutting Mill
The Rotoplex granulator is a real classic in our range of machines and is upgraded continually to accommodate the latest technology. In the production of lithium-ion batteries, it can be used for a variety of tasks -from pre-crushing graphite for the battery anode to various recycling tasks. The Rotoplex is an efficient all-in-one solution that achieves high yields and recycling rates thus ensuring minimal product waste.
Applications
- Anode materials: graphite, copper
- Cathode materials: aluminium foil
- Recycling: cutting cathode and anode in preparation for the separation of the black mass, pre-crushing for further processing with the UPZ fine impact mill or the AFG fluidised bed opposed jet mill
Principle of operation
The Rotoplex cutting mill is characterised by an extremely powerful and robust design, incorporating the unique cross-scissor cut rotor. The rotor guarantees optimal material distribution, a sharp cut and a low-dust product at maximum cutting performance. A housing made of fracture-resistant cast iron ensures that even in heavy continuous use, Rotoplex granulators do their job reliably over many years.
Your advantages with the Rotoplex cutting mill
- Unique cross-scissor cut rotor for energy-efficient cutting, no residues of copper and aluminium, homogeneous distribution of foil flakes without small parts
- Even distribution of the product
- Knives can be replaced individually in segments for easier maintenance and cleaning. This also reduces maintenance costs and the cost of spare parts
- Assurance of good separability of black mass and foil
- Possibility of introducing an inert gas to protect the material and prevent combustion (ATEX)
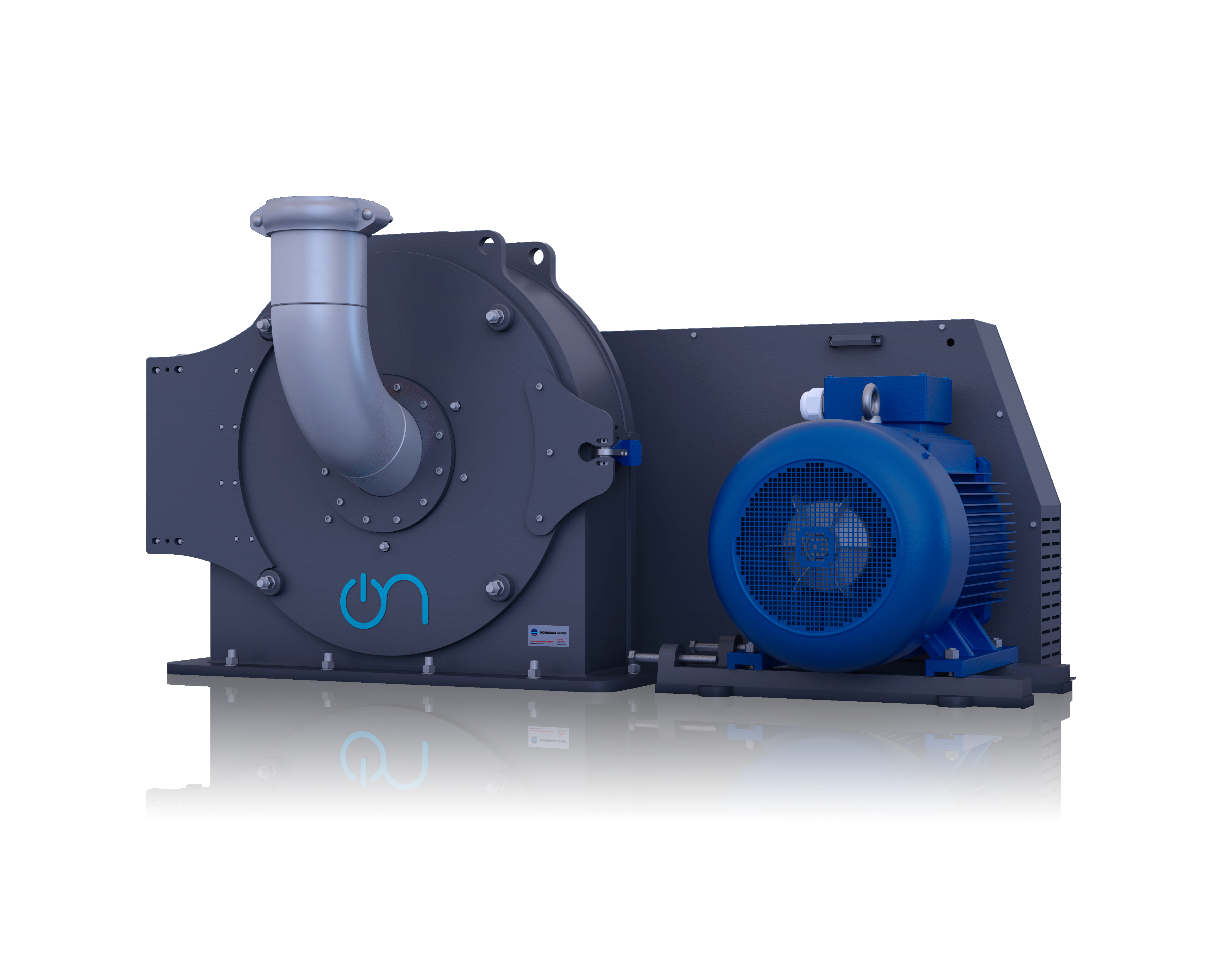
Ultraplex UPZ Fine Impact Mill
The Ultraplex UPZ fine impact mill is a versatile size-reduction system with exchangeable grinding elements. Possibilities include beater disc, pin discs, swing beaters and plate beaters, sieves and grinding tracks. Depending on the grinding element, finenesses between 50 µm to approx. 5 mm can be achieved. Which grinding element you choose for pre-milling synthetic graphite depends on the feed size. For direct scrap recycling of production scrap plate beaters are recommended.
Application
- Pre-milling of synthetic graphite: pre-process before grinding with ZPS classifier mill for graphite pieces larger than 4 cm
- Standard recycling solution for delamination to separate cathode material from aluminium foil
Principle of operation
UPZ fine impact mills are universal in operation for the size reduction of soft materials up to 3 on the mohs scale. The product is fed centrally via the mill door. The machine housing is designed to accommodate all the different milling elements. The fineness is adjusted by selection of the corresponding size reduction elements and as a function of the machine speed; the belt pulley needs to be exchanged when a larger machine size is being selected. If the mill is used for direct recycling of production scrap, downstream classifying is necessary.
Your advantages with the UPZ fine impact mill
Pre-milling of synthetic graphite:
- Relatively small size: saves space
- High throughputs
- Energy-saving grinding process: pre-milling reduces energy consumption during the grinding process with the ZPS classifier mill
- Less wear and tear on the ZPS classifier mill
Direct recycling of production scrap:
- High degree of separation
- High throughput
- Continuous and simple process
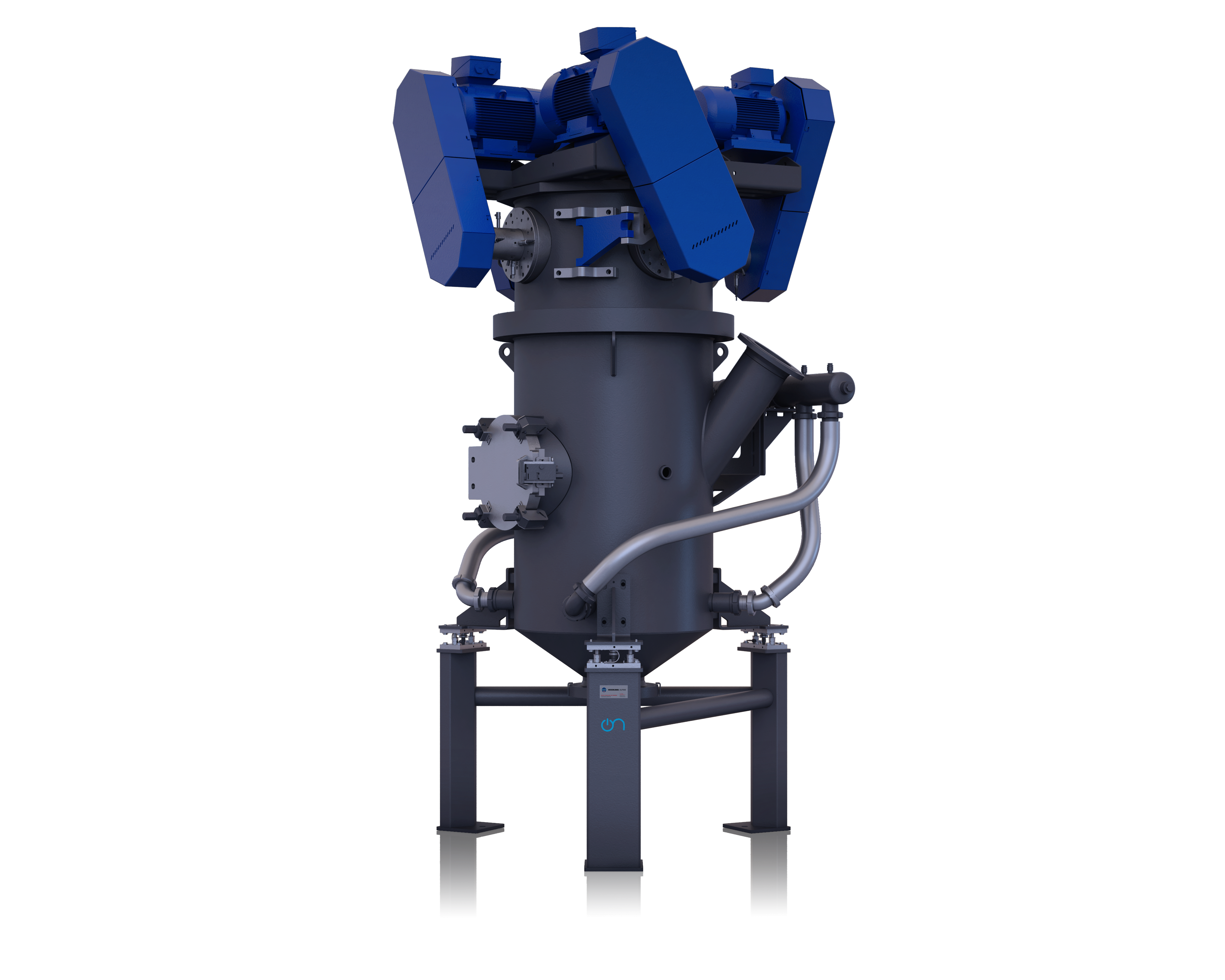
AFG Fluidised Bed Opposed Jet Mill
The AFG fluidised bed opposed jet mill is used in various process steps during battery manufacturing. It is used for the production of powders with a steep particle size distribution and sharp top size limitation in the range < 5 µm to 200 µm.
Applications
- Grinding of lithium and lithium compounds
- Grinding of silicon and silicon compounds
- Grinding of rare earths (with highly flammable properties)
- Delamination: separation of cathode material from aluminium foil or anode material from copper foil
Principle of operation
Jet mills are impact mills which are used to achieve maximum fineness values at maximum product purity. Such particle sizes can only be achieved in connection with an air classification process step . Fluidised bed opposed jet mills are equipped with a dynamic deflector-wheel classifier.
In a fluidised bed opposed jet mill, the product is fed via a feed lock. A product fluidised bed then forms in the grinding chamber, which is fluidised by the gas jets. From there, the particles enter the gas jets and are accelerated. They collide with each other again and again and are thus comminuted. A classifier wheel rejects those particles that are still too large and conveys them back into the fluidised bed. The particles that are fine enough are separated from the grinding gas by a separator or dust filter.
The fineness of the product is adjusted via the speed of the classifier wheel. All-important is a high product loading of the nozzle jets in order to obtain a high particle concentration and thus high impact probabilities. The unique Megajet nozzles were specifically developed for this purpose. The product level in the machine is controlled by load cells or by monitoring the current loading of the classifier drive.
Your advantages with the AFG fluidised bed opposed jet mill
Production of active cathode and anode materials
- Wear protection with different ceramics (standard for grinding lithium, optional for grinding silicon and rare earths) : no contamination of the product. In addition, the effort for maintenance and service is reduced and thus also the downtimes.
- Easy accessibility for easy cleaning and maintenance
- High throughputs with low pressures: energy-efficient production of fine powders with little energy
- Design for contamination-free processing
- Gas- and dust-proof design protects staff and the work environment from toxic lithium compounds and protects the materials from exposure to moisture
- Integrated classifying wheel(s) arranged horizontally in the classifier top section. The results are a steep particle distribution and an exact top cut. These are necessary for optimum coating thicknesses for electrodes.
- When processing silicon and silicon compounds, the system can be run with nitrogen or argon. This reduces costs. Due to the lack of oxygen, the silicon cannot oxidize. This makes it more active and requires less space in the anode. It also makes it possible to process rare earths.
Direct recycling of production scrap
- High degree of separation prevents loss of valuable raw materials. The cathode or anode material is very pure and contains no traces of aluminium or copper foil.
- Separation from the foil takes place in the cyclone: no additional classifying necessary
- Gas- and dust-proof design protects the materials from moisture
- If the system has to be operated with nitrogen it can be run in a closed loop. This keeps the loss of nitrogen low and reduces costs.
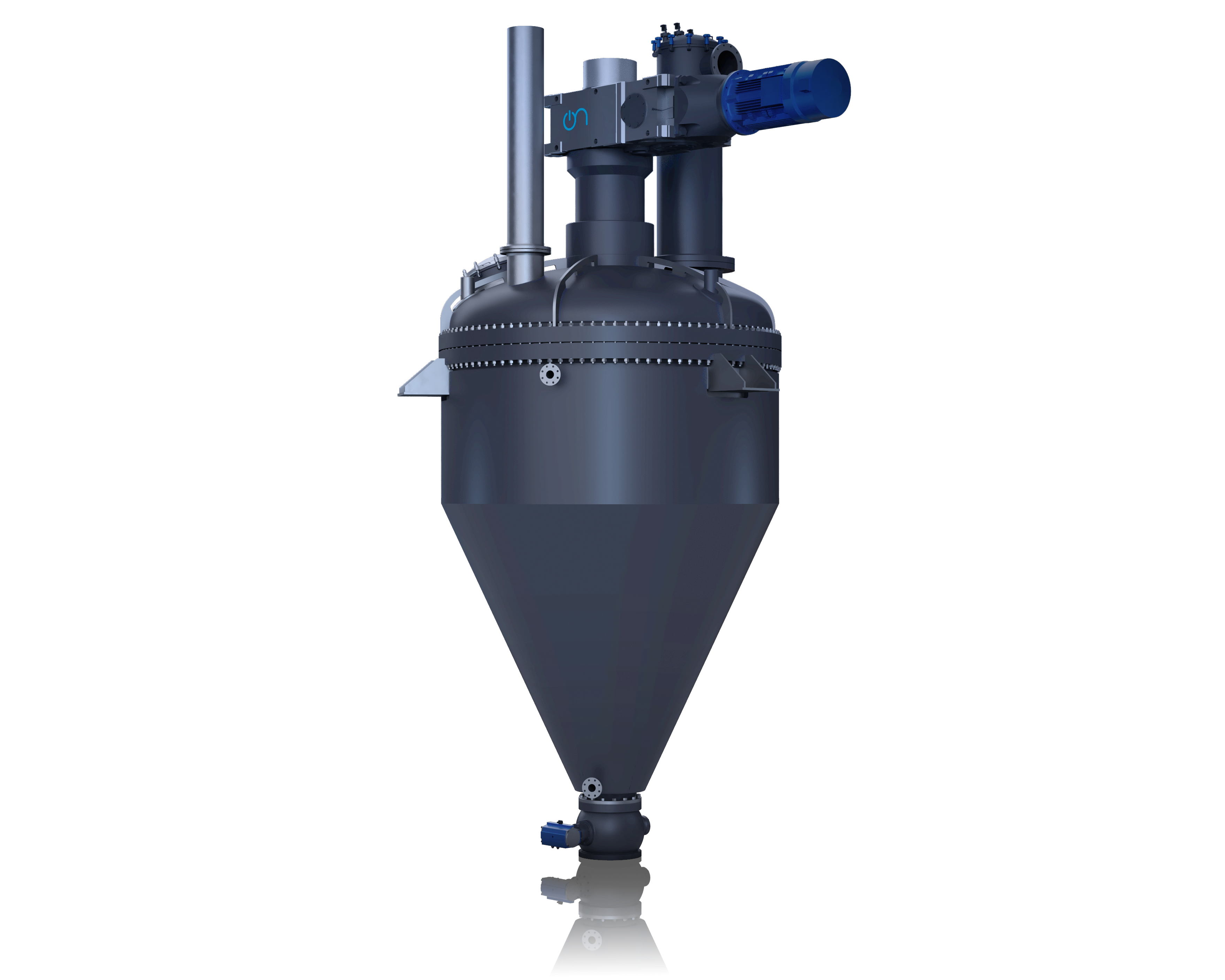
CPD Conical Paddle Dryer
Water is very undesirable in battery materials. Therefore, drying the materials is an integral step in the production process of lithium-ion batteries. The CPD conical paddle dryer is excellent in handling base material at higher temperatures, resulting in high heat transfer rates.
Applications
- Lithium
- Recycling of lithium-ion batteries
Principle of operation
The CDP conical paddle dryer consists of a conically shaped vessel equipped with a central paddle rotor. As it rotates, the rotor creates a combination of vertical and axial motion inside the vessel. The paddles gently guide the product to the surface of the batch where it is dispersed, and gravity in the center of the dryer pushes the product back down, creating continuous motion throughout the drying cycle, even at low speed.
Thanks to the vacuum inside the conical paddle dryer, vapour can be removed at low temperatures, making the CPD ideal for drying heat-sensitive products. The vapours are removed by a dust filter mounted on top of the vessel. This prevents the dust from entering the vacuum system.
The CPD is equipped with a condenser with a solvent recovery tank, which can be installed before and/or after the vacuum pump.
Your advantages with the CPD conical paddle dryer
- Conical paddle dryer for low shear mixing and drying with a high heat transfer rate and lower residual moisture
- Central paddle rotor for low maintenance and easy discharge: As there are no bearings and thus no lubricants in the product zone, contamination of the product is impossible.
- Full vacuum execution to achieve PPM levels of moisture. The result is a high-quality product with low end moisture.
- Bottom outlet for an easy, fast and full discharge of the dryer and easy cleaning of the machine. Therefore, a high yield is guaranteed.
- Containment: The CPD operates at full vacuum, which makes the process safe. Operators and environment are protected, and the dryer is suitable for an ATEX environment. Furthermore, there is no contamination, and the raw materials are protected to prevent reactions.
- Operating temperature: The CPD can be operated at high temperatures. This makes it possible to remove and recover the electrolyte for the recycling of batteries, allowing separation of the black mass from the current collectors.
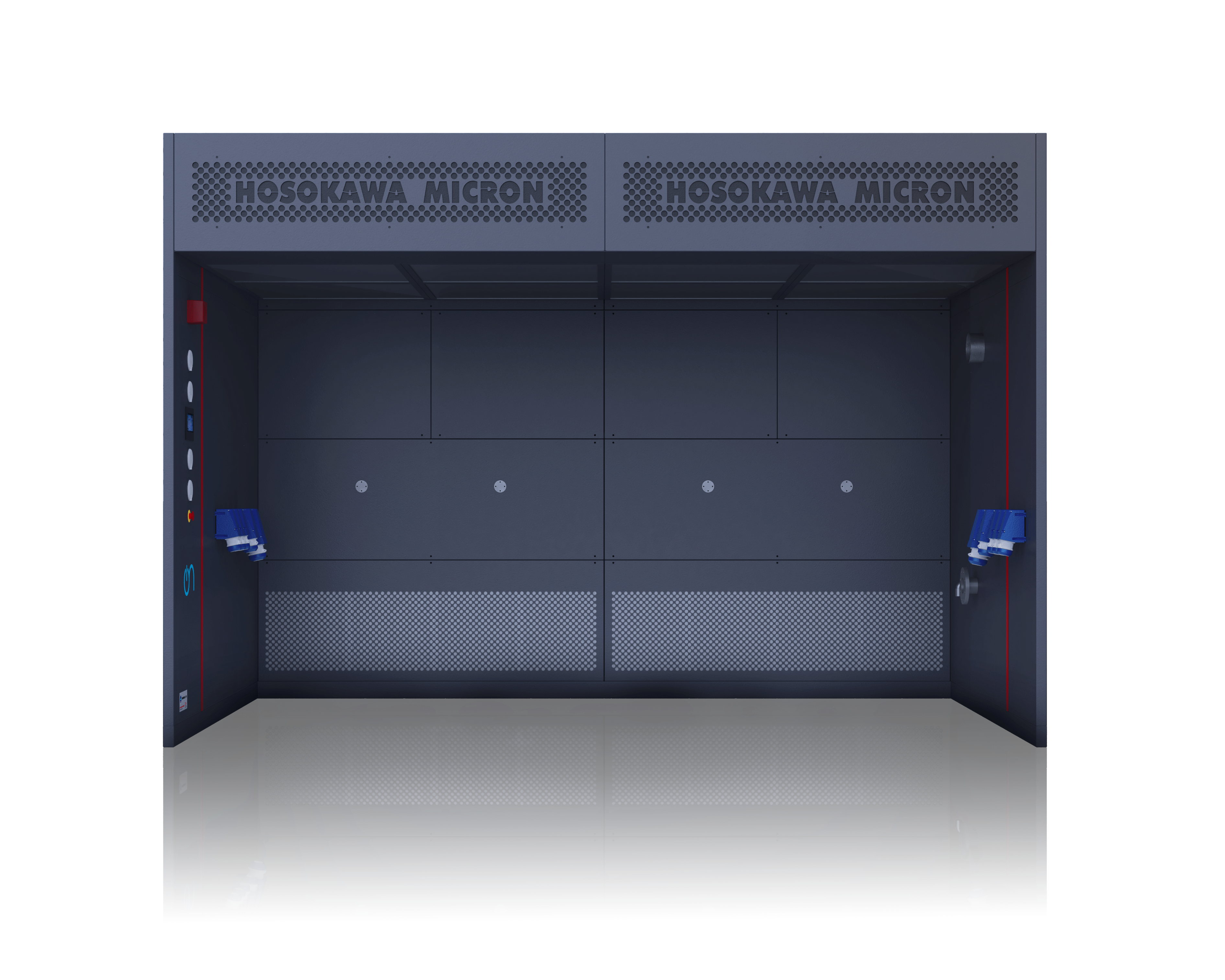
Downflow Booth
Downflow booths (single pass or recirculation) offer a pragmatic and ergonomic solution to containment requirements during the production of battery materials. Downflow Booths are used particularly where hazardous, toxic or sensitizing powders are handled, for sampling, weighing, sieving or conveying of powders, and containing individual process steps in an existing production line (factory) lay-out from lab scale to production scale.
Applications
- Containment of hazardous products during battery production
- Protection of personnel and product protection
Principle of operation
The air recirculation system ensures complete safety for personnel as a conditioned downflow of air passes vertically from the booth’s ceiling inlet plenum pushing any dust or vapours downwards and away from the operator’s breathing zone.
The air is extracted from the booth via low level grills mounted in the rear wall. The exhaust air is taken through a series of filters prior to recirculation into the booth.
Your advantages with the downflow booth
- Ergonomic access: The downflow booth is open fronted, this offers unrestricted operator access to the target operation (i.e. no physical impediment offered by the containment equipment).
- Flexibility to handle a large range of container types
- Capability to integrate additional process equipment
- It will allow clients to meet their safety needs without having to compromise on process efficiency.
- Multi-stage filtration with final HEPA grade
- Guaranteed operator exposure levels of <100 ug/m3: subject to good SOP
- ATEX design to meet standards and safety requirements
- Safe Change Filter Housings limit exposure of harmful products to the environment as potentially hazardous material is captured in filters that can be exchanged safely.
- Recirculation mode for handling powders and pharmaceuticals assures operator protection
- Single pass mode for hazardous products and solvent handling stops potentially harmful products coming into contact with operators
- Low noise due to improved fan selection and booth plenum design
- Controlled entry and exit airlocks to maintain air pressure control between adjoining rooms (generally with different air cleanliness standards)
- 5D High Containment Screens can meet client expectations for an even lower OEL. These are flexible and moveable screens which enforce physical separation between operator and material.
- Temperature cooling/heating packages to meet requirements for a certain ambient room temperature: The booth provides a constant temperature both for the operators and for products which require a defined ambient temperature.
- 70% energy savings, energy conservation mode of operation, LED lights, high efficient fan sets
- Modular design and plug & play system make for easy commissioning and fast installation and offers shorter lead times
- Easy cleaning saves time during production and reduces costs for operating staff. There is also less contamination from previous products being handled in the booth.
- Meets HSE standards and legal requirements to protect the operators
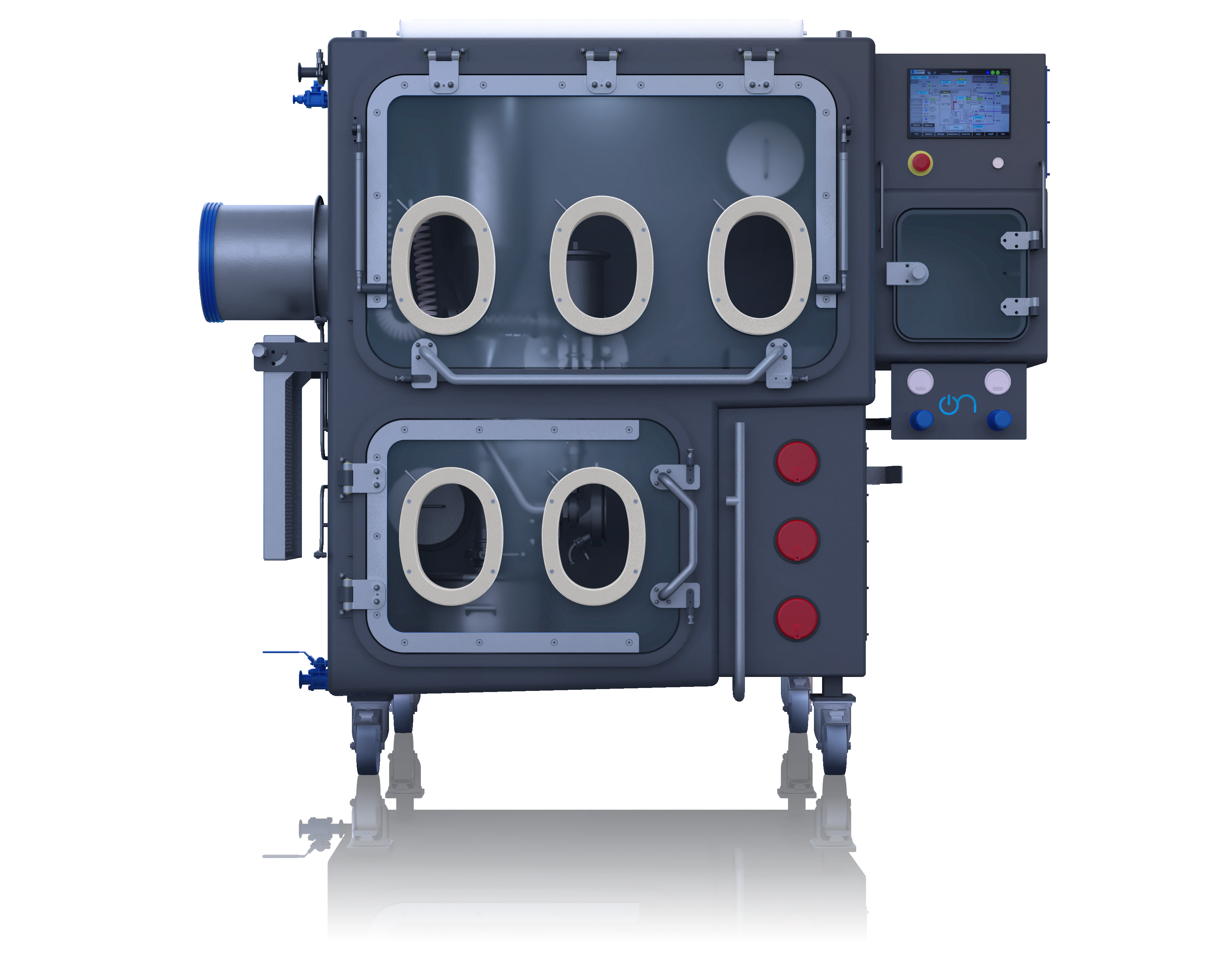
Isolators (Gloveboxes)
Isolators fulfill two important containment functions in the manufacturing process of battery materials. Firstly, they protect operators from the often toxic or carcinogenic raw and active materials. Secondly, they protect the products from contamination and thus increase product quality. Hosokawa ON provides isolators (gloveboxes) for these purposes that can be extended (additional glove-ports and sizes) depending on individual requirements and process workloads
Designed for manual and automated handling and processing, Hosokawa ON’s isolators are available in single and multi-cell variants for processes including milling, micronising, dispensing, sampling and product pack-off.
Applications
- Containment of hazardous products during battery production . Lithium battery materials include cathode materials, anode materials, conducive materials, graphene or nanomaterials etc.
- Product protection
- Safe and stable process conditions including inert oxygen and moisture free atmosphere, gas purification systems
- Integrate third party equipment (ovens, solvent purification systems)
Principle of operation
The isolator incorporates an extract system which maintains a negative pressure internally to ensure that any dust is contained inside the chamber and drawn into the extract filters.
Your advantages with an isolator
- Flexible isolator solutions (bespoke) for a high level of protection as well as easy cleaning, maintenance and disposal
- Window system (lift-up glass or acrylic), hinged and with an inflatable seal, for easy access to the equipment inside the glovebox
- Safe filter change options to limit the exposure of harmful products to the environment: Potentially hazardous material is captured in filters that can be exchanged safely
- Multi-chamber isolator for the highest level of containment:
- Example: upper isolator houses the fill head and the lower chamber houses the drum, customers obtain a dedicated extract and handling system with the option to clean the drum before disposal, ensuring optimal operator protection.
- Big bag discharge glovebox: big bags can be manually discharged in a glovebox to protect operators and the product.
- Glove Safe Change System: Gloves are safely exchanged without bringing the operator into contact with the product. The change operation is easy and quick without contamination of the product.
- Pass Box / Airlocks for complete isolation limiting exposure of the material to the environment
- Half Suit Isolators for improved operator access & ergonomics. The breathing air is filtered to protect the operators.
- Integrated engineering: Hosokawa powder processing equipment can be re-designed for installation inside Gloveboxes/isolators for a more bespoke processing response and delivering an improved ergonomic solution.