Lithium compounds: Processing solutions for your company battery production
Lithium is a soft, silvery-white alkali-metal. It has the highest electrochemical potential of all metals and is therefore an indispensable component in lithium-ion batteries for electromobility and consumer electronics. It is the most important active material in the cathode and determines the performance of the battery. In battery production, lithium is used exclusively as a lithium compound such as lithium nickel manganese cobalt oxide (NMC/Li-NMC), lithium nickel cobalt aluminium oxide (NCA), or lithium iron phosphate (LFP).
The processing of lithium compounds is necessary in battery production in order to make optimal use of the valuable raw materials. ON has developed technologies that meet industry requirements and help customers obtain high-performance cathode materials for lithium-ion batteries.
Advanced lithium for high-performance cathode active material
To produce the best possible active materials for the cathode, a number of factors are important. A steep particle size distribution is important, as it determines the performance of the battery. The batteries can be charged faster, enjoy a longer service life and higher capacity. Additionally, the lithium must be free of moisture and contamination (especially iron and other metals).
ON meets the challenges of handling and processing lithium battery materials with a variety of solutions from drying to grinding and mixing.
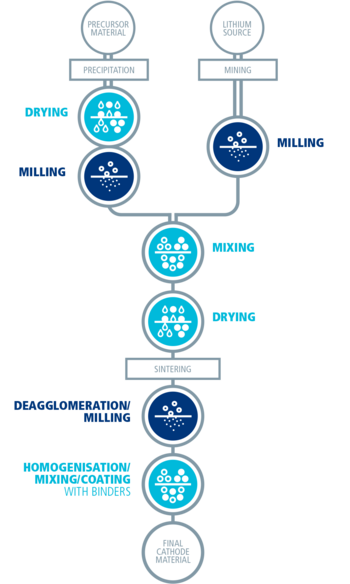
Increasing the efficiency of cathode active materials
To obtain high-performance lithium battery materials, several process steps must be optimised. Especially important is the particle size distribution of the raw materials, homogeneous mixture and good quality coating.
ON presents technologies to improve the performance of battery materials in every single process step - from milling to mixing and coating.
Lithium processing
The main raw material for active cathode materials is lithium. Lithium can be extracted from salt lakes or mined. Regardless of the source of the lithium, it must be ground to the desired particle size. Classifier mills and fluidised bed opposed jet mills are able to handle large throughputs and achieve a steep particle size distribution. Additionally, they can achieve an exact top cut and therefore a high product quality.
Then the particles are mixed, dried and sintered to form battery/cathode active material. During the sintering process, hard agglomerates are formed. Therefore, a deagglomeration or milling step is required before mixing the active material with binders and carbon black to from the final cathode. Finally, it is applied in layers to aluminium foil to form the cathode of a lithium-ion battery.
Drying raw materials used in batteries
The hygroscopic precursor materials such as nickel, manganese or cobalt oxide are produced via a calcination process. To be further processed into active materials for lithium-ion batteries, they have to be dried to eliminate moisture. The Drymeister DMR flash dryer (for lithium, nickel, cobalt and manganese), the CPD conical paddle dryer or the Nauta dryer (both for lithium) are best suited here to remove moisture from slurries and filter cakes.
Grinding high-performance lithium battery materials
For further processing of the active materials, a fine powder with homogeneous particle size distribution is required. Therefore, ultra-fine grinding of the active substances is the next process step. Two mills from ON are particularly suitable for ultra-fine grinding: the air classifier mill ACM and the AFG fluidised bed opposed jet mill AFG.
Drying the lithium compounds in battery production
Water is very undesirable in battery materials. Therefore, ON has several dryers, both batch and continuous to get rid of any moisture. As with drying the cathode precursor materials, this can be achieved with the Drymeister DMR flash dryer (continuous drying), the Nauta dryer or the CPD conical paddle dryer (both batch drying)
Mixing and coating in lithium processing
To increase the cycle stability of the cathode material, coating of the NMC particles is necessary. High-shear mixers as Cyclomix and Nobilta (batch mixing) do not only achieve a homogenous mixture, but also form a strong coating of other materials, such as carbon black and binders around the precursor to improve conductivity. The purity of the coating also is an important issue.
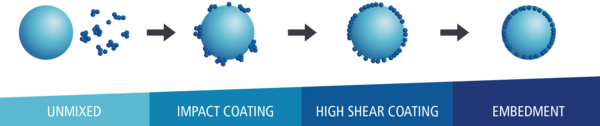
Containment in lithium processing
Containment solutions are necessary in lithium processing plants to prevent both contamination of the product and to protect the surroundings and operators, as some active materials are partly carcinogenic. Therefore, the systems must be gas-tight and dust-free. Operator safety is also an important consideration when handling battery materials. Depending on the product and the required OEB (Occupational Exposure Banding) level, the Hosokawa Micron Group offers a range of standard and bespoke containment equipment to complement its drying, mixing, milling and particle design equipment.
Complete systems for your industrial battery production
Lithium-ion refinery is a complex process in which various process steps must work together in order to produce high-performance batteries. In this, customers benefit from the combined knowledge of ON. Companies throughout the Hosokawa Micron Group specialise in different technologies and work hand in hand to provide you with the optimum solution for your battery production. Contact us for more information!
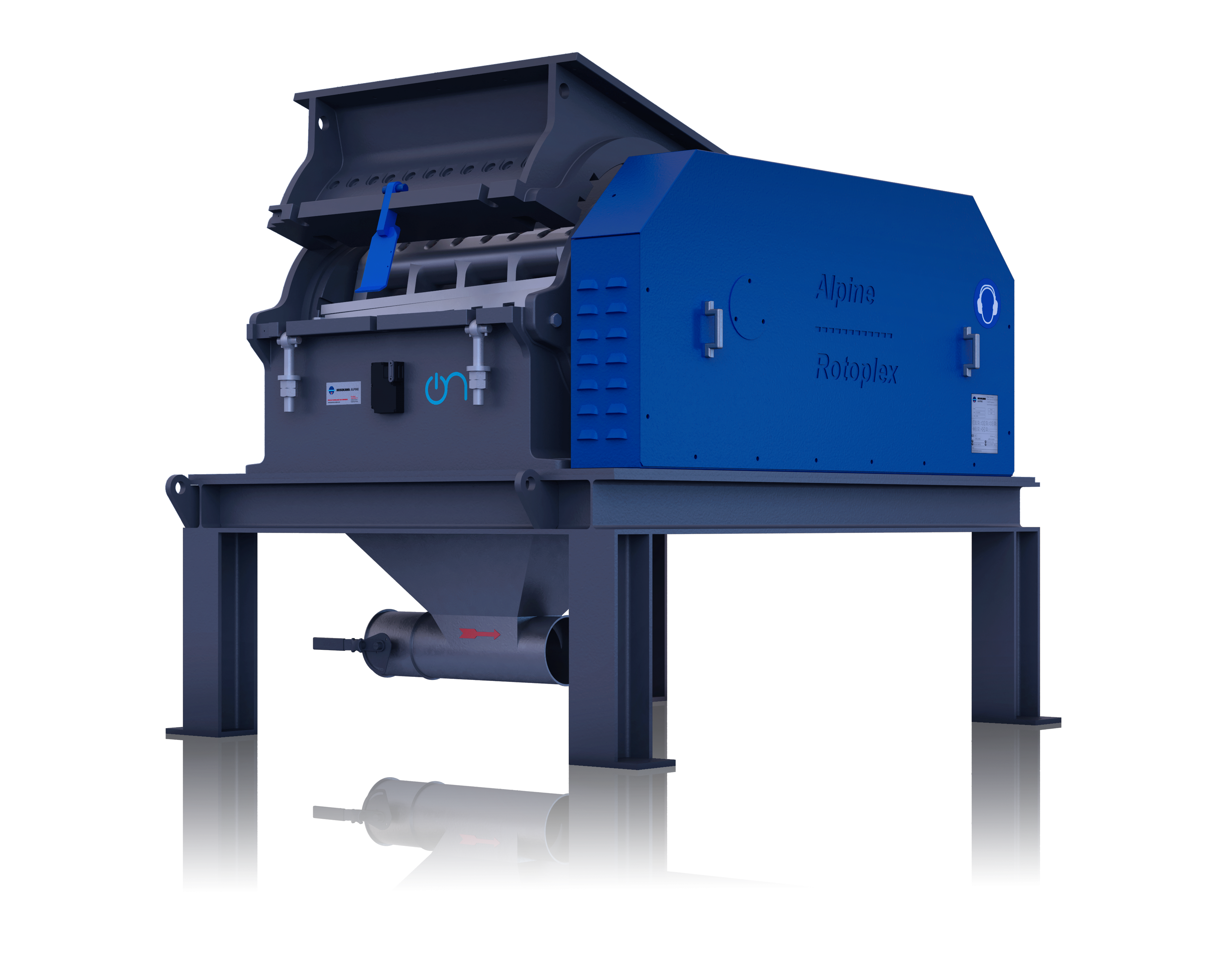
Rotoplex Cutting Mill
The Rotoplex granulator is a real classic in our range of machines and is upgraded continually to accommodate the latest technology. In the production of lithium-ion batteries, it can be used for a variety of tasks -from pre-crushing graphite for the battery anode to various recycling tasks. The Rotoplex is an efficient all-in-one solution that achieves high yields and recycling rates thus ensuring minimal product waste.
Applications
- Anode materials: graphite, copper
- Recycling: cutting cathode and anode in preparation for the separation of the black mass, pre-crushing for further processing with the UPZ fine impact mill or the AFG fluidised bed opposed jet mill
Principle of operation
The Rotoplex cutting mill is characterised by an extremely powerful and robust design, incorporating the unique cross-scissor cut rotor. The rotor guarantees optimal material distribution, a sharp cut and a low-dust product at maximum cutting performance. A housing made of fracture-resistant cast iron ensures that even in heavy continuous use, Rotoplex granulators do their job reliably over many years.
Your advantages with the Rotoplex cutting mill
- Unique cross-scissor cut rotor for energy-efficient cutting, no residues of copper and aluminium, homogeneous distribution of foil flakes without small parts
- Even distribution of the product
- Knives can be replaced individually in segments for easier maintenance and cleaning. This also reduces maintenance costs and the cost of spare parts
- Assurance of good separability of black mass and foil
- Possibility of introducing an inert gas to protect the material and prevent combustion (ATEX)
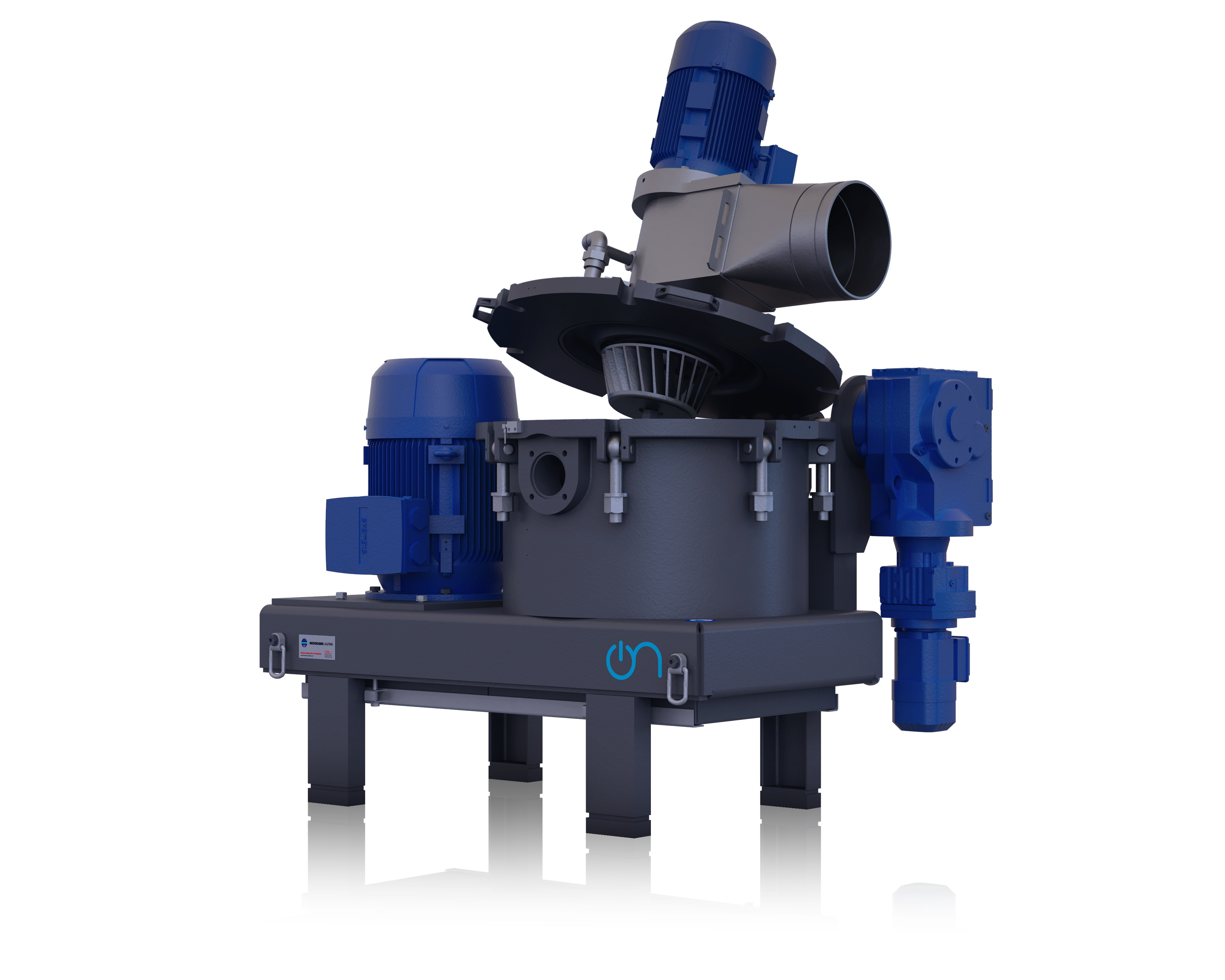
ACM-BC Classifier Mill
The ACM-BC is a fine impact mill with a built-in classifier. It can achieve very high finenesses and was specially developed to grind and classify materials that need to be processed without any metal contamination, which is the case with cathode materials for the production of lithium-ion batteries. This is why all machine parts that come in contact with the powder are made of ceramics. The mill and classifier structure is thoroughly simplified, resulting in high reliability.
In battery production, fine grinding of the raw and active materials is very important – a task that the ACM-BC is well-equipped for.
Applications
- Grinding and classifying of lithium compounds: LCO, NMC, NCA, etc.
Principle of operation
The product is pneumatically fed into the ACM classifier mill. Size reduction is achieved bby the mechanical impact on the product between the rotating grinding elements and the stationary liner. The conveying air transports the milled particles to the classifier wheel.
A characteristic feature of the ACM is the integrated dynamic classifier. The product-air mixture is evenly fed by the rotating classifier wheel to the rotating classifier. The product is separated in the classifying zone into a coarse fraction and a fine fraction. The coarse material is rejected by the classifying wheel and returned to the grinding zone for further comminution. The fine material passes the classifying wheel and exits the grinding chamber. The cut point is set via the speed of the classifying wheel, which can be adjusted continuously even during operation.
Your advantages with the ACM-BC classifier mill
- Grinding and classifying operation in one machine
- Steep particle size distribution
- Sharp and easily adjustable precision of top cut
- Contamination-free product
- Easy cleaning and maintenance
- Low specific energy consumption
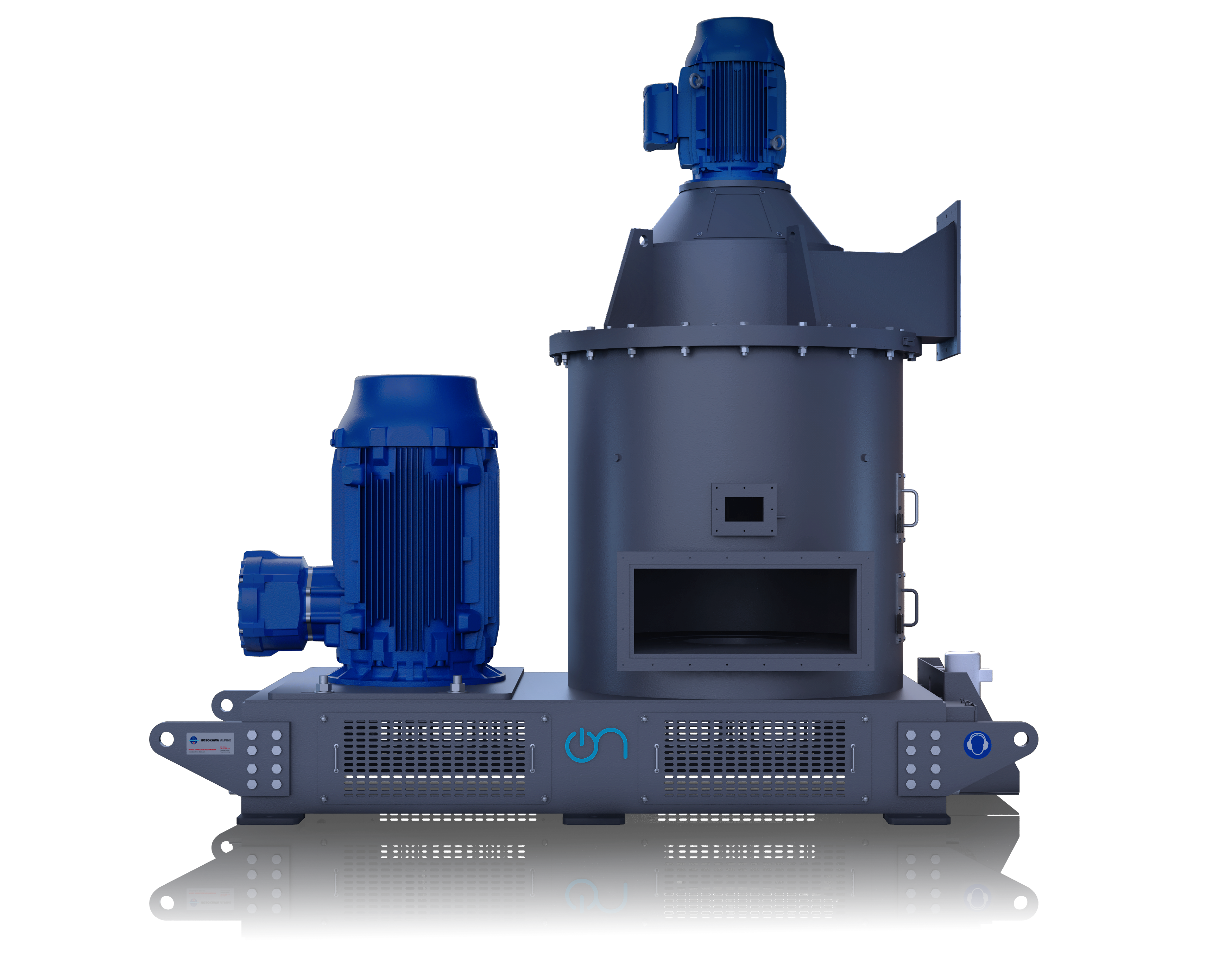
Mikro ACM Classifier Mill
The Mikro ACM® Air Classifying Mill is a fine mechanical impact mill with an integrated classifier. It was designed to grind a wide range of materials down to D97 < 20 µm. In the production of lithium-ion batteries, it is used for grinding and micronizing both cathode and anode materials.
Applications
- Grinding of lithium carbonate
- Grinding of coke
- Micronizing of graphite
Principle of operation
The product is pneumatically fed into the Mikro ACM® Air Classifying Mill. Size reduction is achieved by the impact of the product on the rotating grinding elements and against the stationary liner. The grinding zone is coupled with an internal dynamic classifier which controls the end-product particle size via recirculating the coarse particles back into the grinding zone. These particles are recirculated through the grinding and classification zones until fine enough to pass through the classifier, and captured downstream via cyclone or filter. The cut point is set via the speed of the classifying wheel and the airflow, which can be adjusted continuously even during operation.
Your advantages with the Mikro ACM® Air Classifying Mill
- Consistent/tight particle size
- Excellent top size control by use of integral, internal classification
- Durability and reliability due to robust construction
- Wear-protected to minimize contamination of the product
- Available in multiple sizes
- Low operating costs
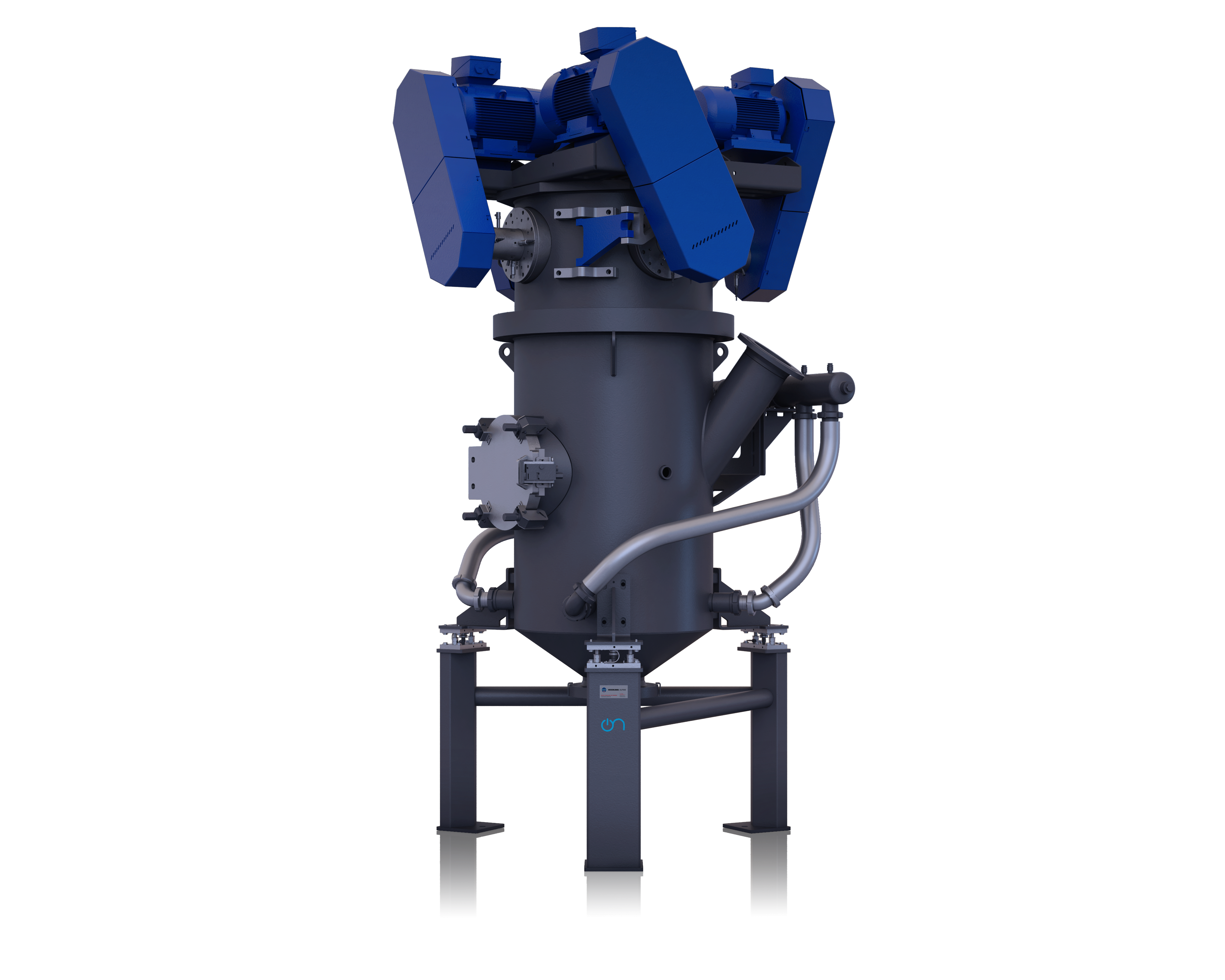
AFG Fluidised Bed Opposed Jet Mill
The AFG fluidised bed opposed jet mill is used in various process steps during battery manufacturing. It is used for the production of powders with a steep particle size distribution and sharp top size limitation in the range < 5 µm to 20 µm.
Applications
- Grinding of lithium and lithium compounds
- Grinding of silicon and silicon compounds
- Grinding of rare earths (with highly flammable properties)
- Delamination: separation of cathode material from aluminium foil or anode material from copper foil
Principle of operation
Jet mills are impact mills which are used to achieve maximum fineness values at maximum product purity. Such particle sizes with a fineness of d50 = 2 to 10 µm can only be achieved in connection with an air classification process step . Fluidised bed opposed jet mills are equipped with a classifier.
A product fluidised bed forms in the grinding chamber, which is fluidised by the gas jets. From there, the particles enter the gas jets and are accelerated. They collide with each other again and again and are thus comminuted. Through conveying air fine particles are transported to the classifier wheel. The classifier wheel rejects those particles that are still too large and conveys them back into the fluidised bed. The particles that are fine enough follow the gas stream into a cyclone or filter where they are separated and collected.
The fineness of the product is adjusted via the speed of the classifier wheel. All-important is a high product loading of the nozzle jets in order to obtain a high particle concentration and thus high impact probabilities. The unique Megajet nozzles were specifically developed for this purpose. The product level in the machine is controlled by load cells or by monitoring the current loading of the classifier drive.
Your advantages with the AFG fluidised bed opposed jet mill
Production of active cathode and anode materials
- Wear protection with different ceramics (standard for grinding lithium, optional for grinding silicon and rare earths): no contamination of the product. In addition, the effort for maintenance and service is reduced and thus also the downtimes.
- Easy accessibility for easy cleaning and maintenance
- High throughputs with low pressures: energy-efficient production of fine powders with little energy
- Design for contamination-free processing
- Gas- and dust-proof design protects staff and the work environment from toxic lithium compounds and protects the materials from exposure to moisture
- Integrated classifying wheel(s) arranged horizontally in the classifier top section. The results are a steep particle distribution and an exact top cut. These are necessary for optimum coating thicknesses for electrodes.
- When processing silicon and silicon compounds, the system can be run with nitrogen or argon. This reduces costs. Due to the lack of oxygen, the silicon cannot oxidize. This makes it more active and requires less space in the anode. It also makes it possible to process rare earths.
- Possible scale-up to several tons per hour due to multi-classifier wheels
Direct recycling of production scrap
- High degree of separation prevents loss of valuable raw materials. The cathode or anode material is very pure and contains no traces of aluminium or copper foil.
- Separation from the foil takes place in the cyclone: no additional classifying necessary
- Gas- and dust-proof design protects the materials from moisture
- If the system has to be operated with nitrogen it can be run in a closed loop. This keeps the loss of nitrogen low and reduces costs.
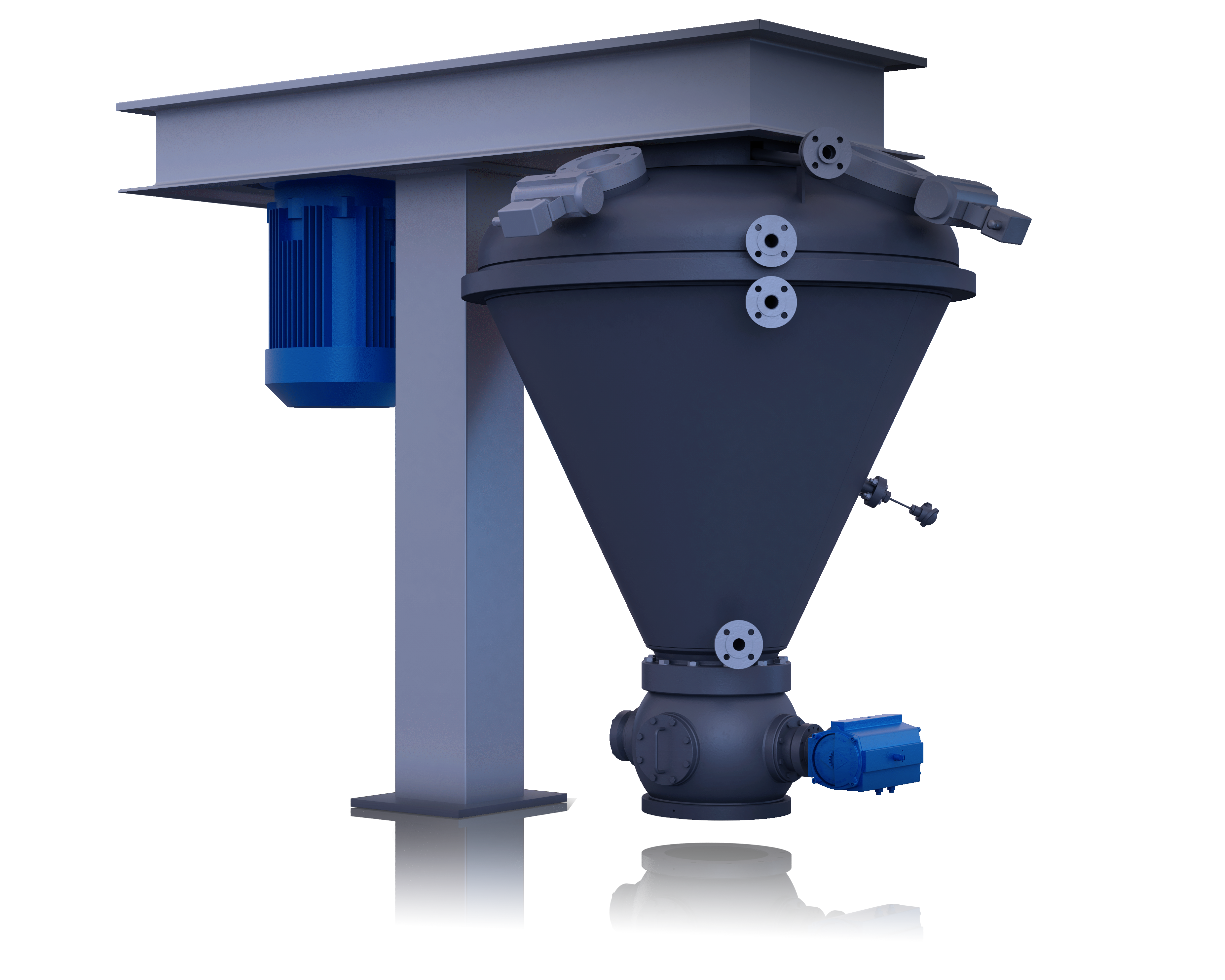
Cyclomix High Shear Impact Mixer
The Cyclomix high shear impact mixer combines high shear and impact mixing in one single machine. The result is a high level of homogeneity in the end product, meeting the stringent demands of the battery production industry.
By achieving homogenous mixing of cohesive powders in ultra-short cycle times, the Cyclomix ensures a full coating of binders and conductive additives around anode or cathode precursors. This process reduces the BET surface area, leading to enhanced battery performance.
With its consistent and high-quality mixing results, the Cyclomix high shear impact mixer is an indispensable tool for battery manufacturers seeking to optimize their production processes.
Applications
- NMC
- Natural graphite
- Synthetic graphite
- Lithium compounds
- LFP
- Nickel
- Cobalt
- Manganese
- CNT (carbon nanotubes)
- Silicon
- Lithium
- Carbon black
- PTFE
- PVDF
- Pitch
- Solid state
- Coating Neodium Iron boron
Principle of operation
The Cyclomix high shear impact mixer consists of a conical mixing vessel, equipped with a central paddle rotor, rotating at tip speeds of up to 30 m/s. The speed of the rotor creates centrifugal forces that push the product against the vessel wall, where the shape of the vessel causes an upward movement. The cover directs the product towards the centre of the mixer and at the top, an impact blade efficiently disperses cohesive powders and liquids.
Advantages of the Cyclomix high shear impact mixer
- Superior efficiency: The Cyclomix features a unique design where the shearing zone extends along the entire vessel wall, not just the bottom. This innovative feature makes the Cyclomix the most efficient high shear mixer available, achieving superior mixing and coating results with lower circumferential speeds and shorter mixing times compared to other mixers on the market.
- Central Paddle Rotor: Equipped with a central paddle rotor, the Cyclomix allows for easy product discharge and requires low maintenance. With no bearings or lubricants in the product zone, the risk of contamination is eliminated.
- Central bottom outlet: The central bottom outlet facilitates complete, easy, and fast discharge of the mixer, making it simple to clean and ensuring a high yield.
- Containment: The Cyclomix operates in an inert atmosphere and under/over pressure, protecting operators and the environment, and making it suitable for ATEX environments. This feature also ensures no contamination of the product, preserving the integrity of raw materials and preventing unwanted reactions.
- Scalability: The Cyclomix is fully scalable, allowing process settings to be reproduced consistently from 1 to 1000 litres of product. This guarantees constant product quality from small-scale to production-scale operations.
- Optional wear protection: Available wear protection options prevent equipment wear and further eliminate product contamination.
- Excellent temperature control: The Cyclomix offers superior temperature control, ensuring optimal product quality throughout the mixing process.
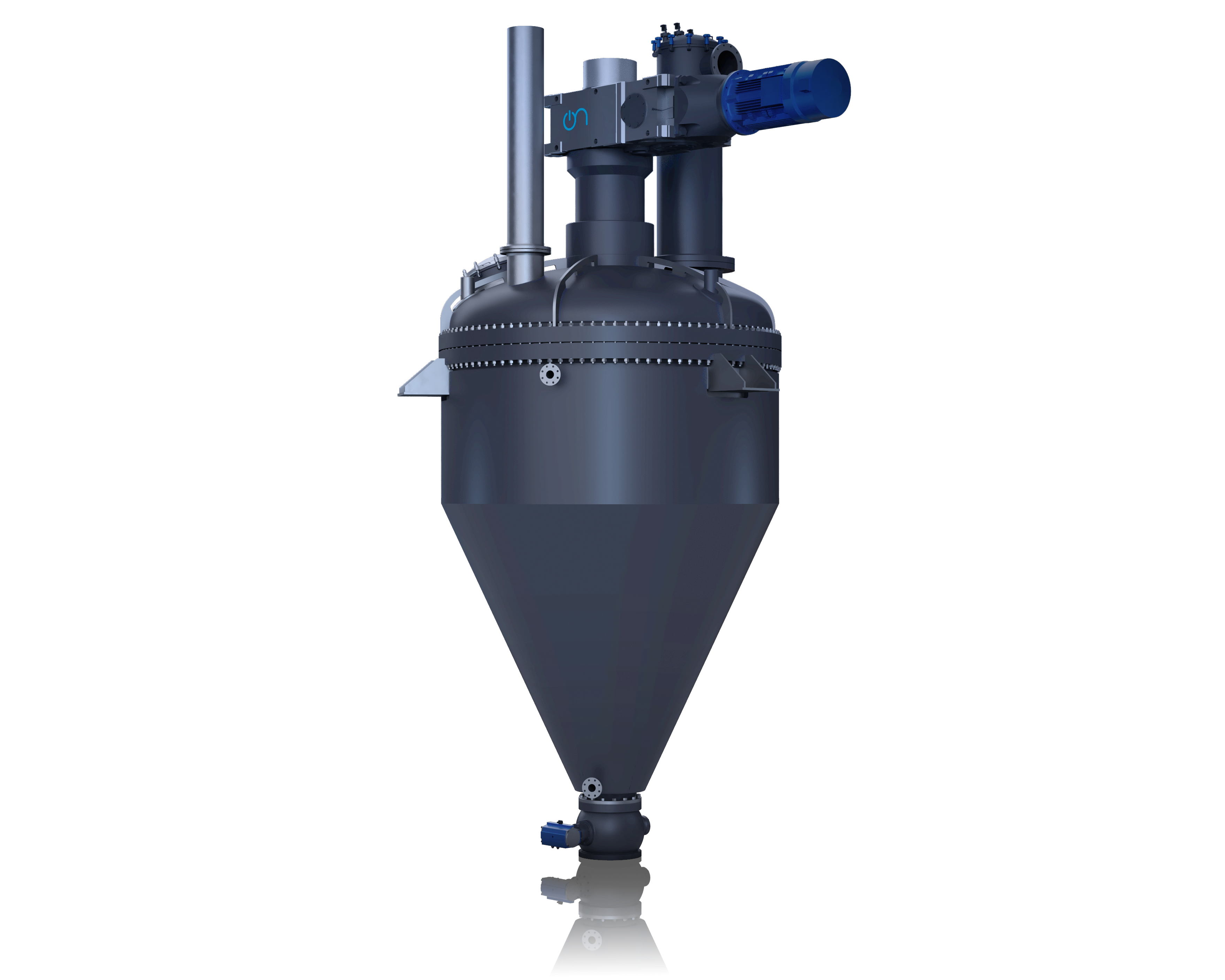
CPD Conical Paddle Dryer
Water is very undesirable in battery materials. Therefore, drying the materials is an integral step in the production process of lithium-ion batteries. The CPD conical paddle dryer is excellent in handling base material at higher temperatures, resulting in high heat transfer rates.
Applications
- Lithium
- Recycling of lithium-ion batteries
Principle of operation
The CDP conical paddle dryer consists of a conically shaped vessel equipped with a central paddle rotor. As it rotates, the rotor creates a combination of vertical and axial motion inside the vessel. The paddles gently guide the product to the surface of the batch where it is dispersed, and gravity in the center of the dryer pushes the product back down, creating continuous motion throughout the drying cycle, even at low speed.
Thanks to the vacuum inside the conical paddle dryer, vapour can be removed at low temperatures, making the CPD ideal for drying heat-sensitive products. The vapours are removed by a dust filter mounted on top of the vessel. This prevents the dust from entering the vacuum system.
The CPD is equipped with a condenser with a solvent recovery tank, which can be installed before and/or after the vacuum pump.
Your advantages with the CPD conical paddle dryer
- Conical paddle dryer for low shear mixing and drying with a high heat transfer rate and lower residual moisture
- Central paddle rotor for low maintenance and easy discharge: As there are no bearings and thus no lubricants in the product zone, contamination of the product is impossible.
- Full vacuum execution to achieve PPM levels of moisture. The result is a high-quality product with low end moisture.
- Bottom outlet for an easy, fast and full discharge of the dryer and easy cleaning of the machine. Therefore, a high yield is guaranteed.
- Containment: The CPD operates at full vacuum, which makes the process safe. Operators and environment are protected, and the dryer is suitable for an ATEX environment. Furthermore, there is no contamination, and the raw materials are protected to prevent reactions.
- Operating temperature: The CPD can be operated at high temperatures. This makes it possible to remove and recover the electrolyte for the recycling of batteries, allowing separation of the black mass from the current collectors.
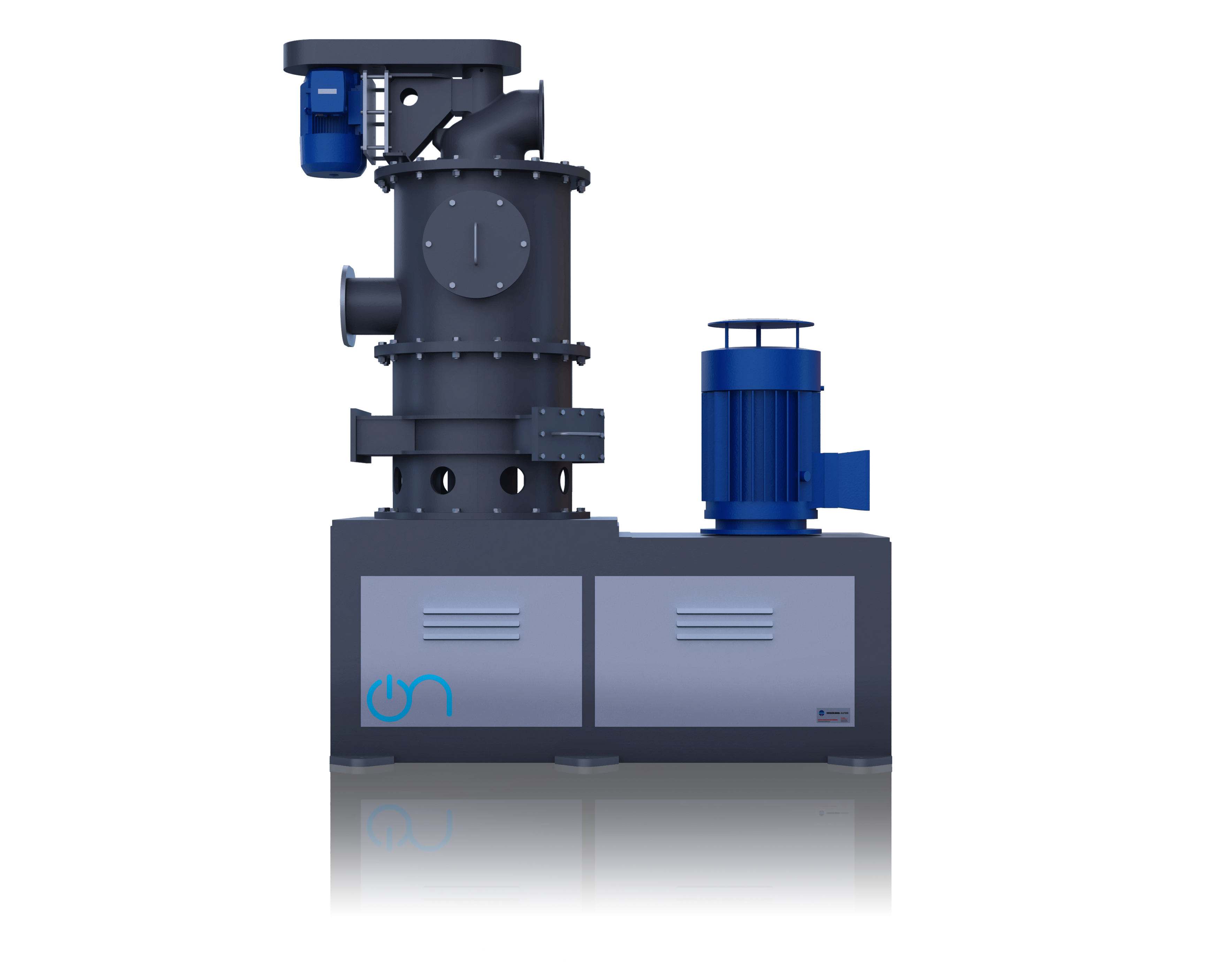
DMR Flash Dryer
The DMR flash drying system was designed to integrate drying, de-agglomeration/milling, and classifying in a single process step, and the first of its kind to be patented. This continuous dryer efficiently handles solids with moisture contents ranging from a few percent to over 80%.
With the right configuration, it can process suspensions, slurries, pastes, filter cakes, and wet powders. Compared to other direct drying technologies, the DMR requires 50% less space and consumes 30-40% less energy per kilogram of evaporated water.
Applications
- NMC
- Lithium compounds
Principle of operation
The wet material is fed into the dispersion and drying section of the dryer using a suitable feeding system. In this section, the rotor disperses the wet material into very fine particles, which are fluidized in the drying chamber by hot gas coming in from the air heater. The temperature of the hot air (or inert gas) can reach up to 650°C.
The dispersion rotor at the bottom of the flash dryer breaks down the wet product, creating a large surface area that allows water (or other solvents) to evaporate instantaneously. Fine and dry particles are then conveyed with the gas stream to the top section of the DMR flash dryer.
At the top, the particles pass through a classifier set to a specific cut point. They are then transported with the exhaust air to a cyclone filter or cyclone scrubber, where the dried powder is separated from the air.
Advantages of the DMR continuous flash dryer
- Ultra-fine regular end product: Produces ultra-fine, uniform end products from slurries, pastes, or filter cakes.
- High evaporation capacity: Achieves efficient evaporation of large liquid volumes due to a high ΔT and excellent dispersion of the wet product in the air.
- Energy efficient: Consumes 30-40% less energy per kilogram of evaporated water compared to other direct drying technologies.
- Compact design: Occupies up to 50% less space than other direct drying technologies.
- Multi-purpose: Handles both filter cake and slurry in the same machine, enabling unlimited mechanical dewatering before the final drying stage.
- Flexible system set-up: Offers open, closed, and recycle system concepts, as well as energy recovery systems, to meet various requirements.
- Wear protection: Includes wear protection options to prevent contamination.
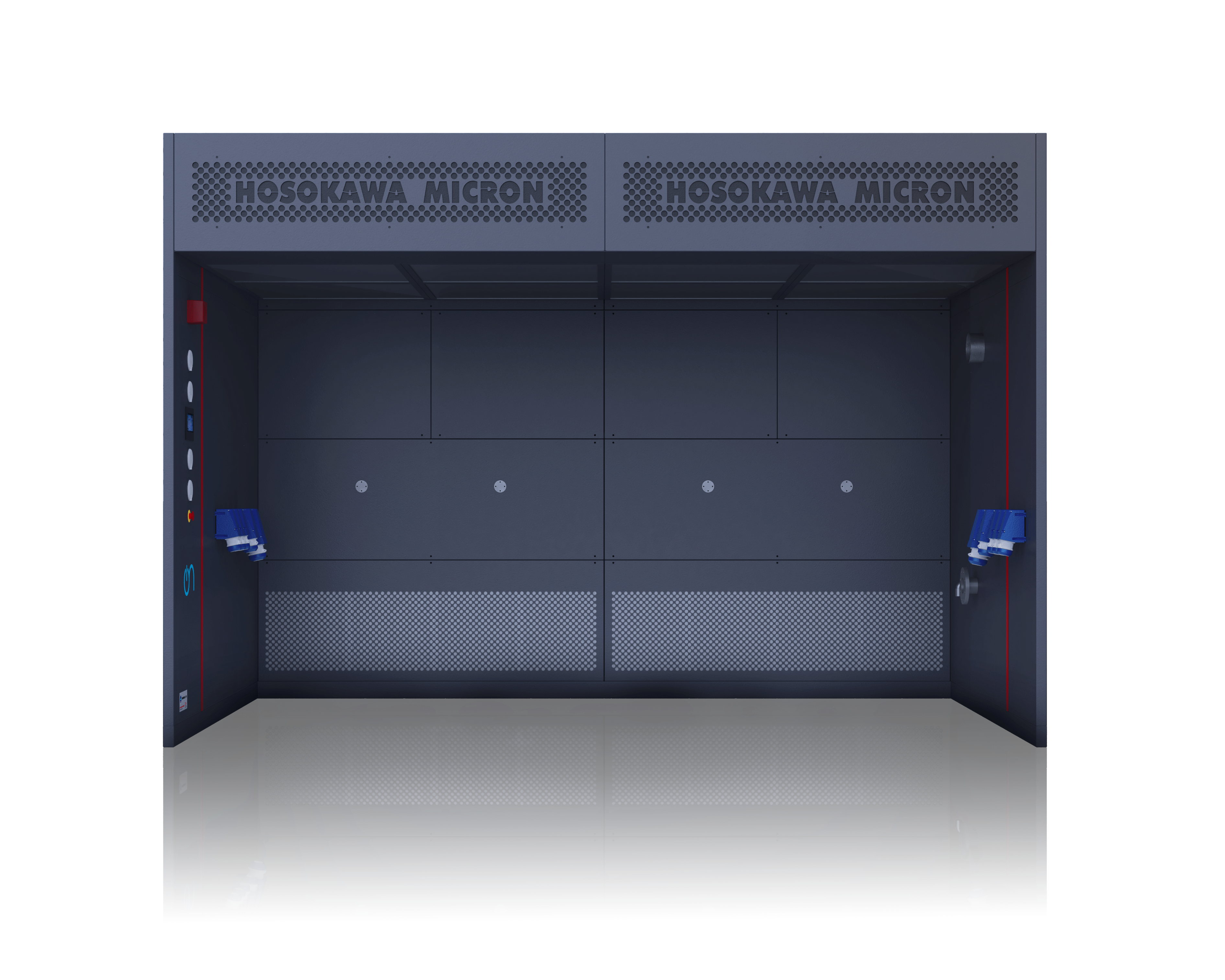
Downflow Booth
Downflow booths (single pass or recirculation) offer a pragmatic and ergonomic solution to containment requirements during the production of battery materials. Downflow Booths are used particularly where hazardous, toxic or sensitizing powders are handled, for sampling, weighing, sieving or conveying of powders, and containing individual process steps in an existing production line (factory) lay-out from lab scale to production scale.
Applications
- Containment of hazardous products during battery production
- Protection of personnel and product protection
Principle of operation
The air recirculation system ensures complete safety for personnel as a conditioned downflow of air passes vertically from the booth’s ceiling inlet plenum pushing any dust or vapours downwards and away from the operator’s breathing zone.
The air is extracted from the booth via low level grills mounted in the rear wall. The exhaust air is taken through a series of filters prior to recirculation into the booth.
Your advantages with the downflow booth
- Ergonomic access: The downflow booth is open fronted, this offers unrestricted operator access to the target operation (i.e. no physical impediment offered by the containment equipment).
- Flexibility to handle a large range of container types
- Capability to integrate additional process equipment
- It will allow clients to meet their safety needs without having to compromise on process efficiency.
- Multi-stage filtration with final HEPA grade
- Guaranteed operator exposure levels of <100 ug/m3: subject to good SOP
- ATEX design to meet standards and safety requirements
- Safe Change Filter Housings limit exposure of harmful products to the environment as potentially hazardous material is captured in filters that can be exchanged safely.
- Recirculation mode for handling powders and pharmaceuticals assures operator protection
- Single pass mode for hazardous products and solvent handling stops potentially harmful products coming into contact with operators
- Low noise due to improved fan selection and booth plenum design
- Controlled entry and exit airlocks to maintain air pressure control between adjoining rooms (generally with different air cleanliness standards)
- 5D High Containment Screens can meet client expectations for an even lower OEL. These are flexible and moveable screens which enforce physical separation between operator and material.
- Temperature cooling/heating packages to meet requirements for a certain ambient room temperature: The booth provides a constant temperature both for the operators and for products which require a defined ambient temperature.
- 70% energy savings, energy conservation mode of operation, LED lights, high efficient fan sets
- Modular design and plug & play system make for easy commissioning and fast installation and offers shorter lead times
- Easy cleaning saves time during production and reduces costs for operating staff. There is also less contamination from previous products being handled in the booth.
- Meets HSE standards and legal requirements to protect the operators
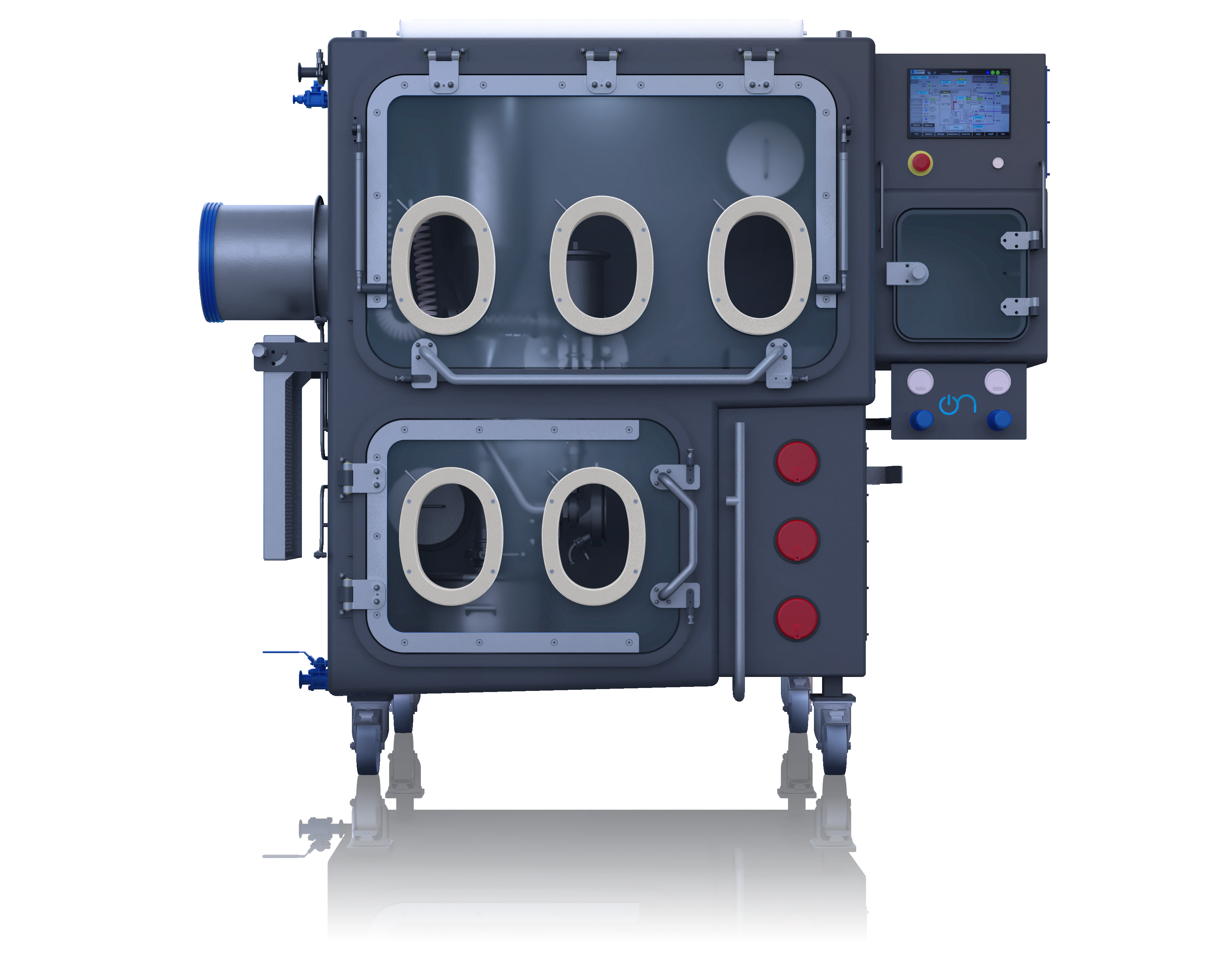
Isolators (Gloveboxes)
Isolators fulfill two important containment functions in the manufacturing process of battery materials. Firstly, they protect operators from the often toxic or carcinogenic raw and active materials. Secondly, they protect the products from contamination and thus increase product quality. Hosokawa ON provides isolators (gloveboxes) for these purposes that can be extended (additional glove-ports and sizes) depending on individual requirements and process workloads
Designed for manual and automated handling and processing, Hosokawa ON’s isolators are available in single and multi-cell variants for processes including milling, micronising, dispensing, sampling and product pack-off.
Applications
- Containment of hazardous products during battery production . Lithium battery materials include cathode materials, anode materials, conducive materials, graphene or nanomaterials etc.
- Product protection
- Safe and stable process conditions including inert oxygen and moisture free atmosphere, gas purification systems
- Integrate third party equipment (ovens, solvent purification systems)
Principle of operation
The isolator incorporates an extract system which maintains a negative pressure internally to ensure that any dust is contained inside the chamber and drawn into the extract filters.
Your advantages with an isolator
- Flexible isolator solutions (bespoke) for a high level of protection as well as easy cleaning, maintenance and disposal
- Window system (lift-up glass or acrylic), hinged and with an inflatable seal, for easy access to the equipment inside the glovebox
- Safe filter change options to limit the exposure of harmful products to the environment: Potentially hazardous material is captured in filters that can be exchanged safely
- Multi-chamber isolator for the highest level of containment:
- Example: upper isolator houses the fill head and the lower chamber houses the drum, customers obtain a dedicated extract and handling system with the option to clean the drum before disposal, ensuring optimal operator protection.
- Big bag discharge glovebox: big bags can be manually discharged in a glovebox to protect operators and the product.
- Glove Safe Change System: Gloves are safely exchanged without bringing the operator into contact with the product. The change operation is easy and quick without contamination of the product.
- Pass Box / Airlocks for complete isolation limiting exposure of the material to the environment
- Half Suit Isolators for improved operator access & ergonomics. The breathing air is filtered to protect the operators.
- Integrated engineering: Hosokawa powder processing equipment can be re-designed for installation inside Gloveboxes/isolators for a more bespoke processing response and delivering an improved ergonomic solution.
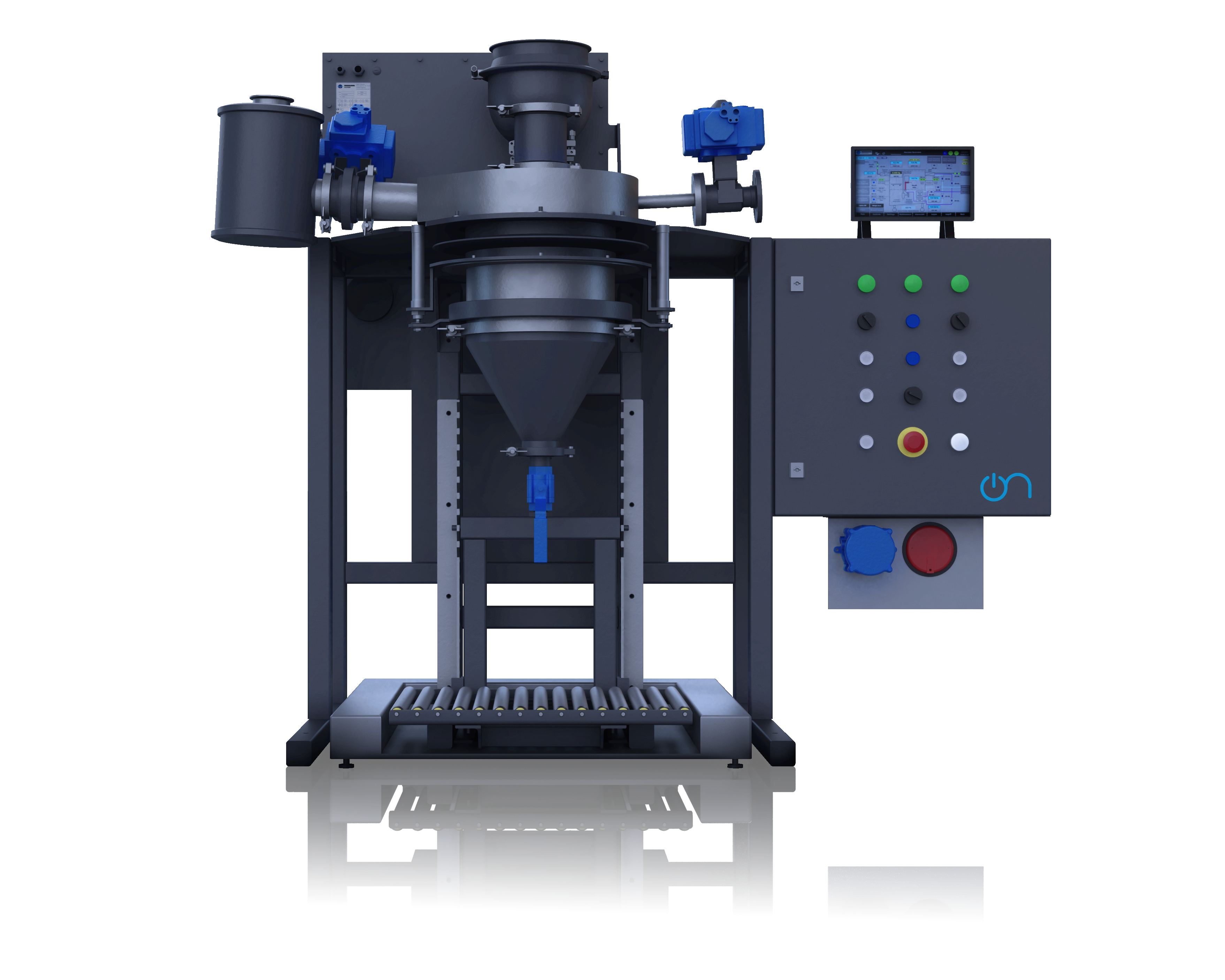
Filling & Weighing Systems
Filling and weighing are important process steps in the production of lithium-ion batteries. Our accurate weight-controlled filling systems maintain the highest standards of hygiene, dust control and product integrity. They deliver accurate, stable and repeatable weight readings and can be designed for use in hazardous areas. They incorporate interchangeable, Stott design inflatable packing heads and integrated weigh platforms to provide automatic control of bulk and dribble filling modes.
Applications
- Filling and weighing various raw and active materials in the production of lithium-ion batteries
Your advantages with our filling and weighing systems
- Our contained filling and weighing system is easy to operate and guarantees a high level of product integrity
- Designed for flexible filling of a range of containers of various sizes including drums with or without liners, IBC’s, FIBC’s, Polybottles, high containment flexible bags
- A single, easy to read, flush mounted control panel display, including continuous weight readout and other process parameters. The system can be connected to the customer’s distributed control system (DCS).
- Compact inward seal that does not come into contact with the product, or alternatively the fill weigh systems can be designed with outward inflatable seal or downward inflatable seal to suite the application.
- A range of dosing devices are available to achieve weighing accuracy during filling, ranging from simple butterfly valves to highly accurate screw feeders depending on material characteristics and accuracies required.
- Secondary containment is provided by enclosing the fill / weigh system inside one of Hosokawa’s Horizontal Laminar Flow Booths designed for the application or alternatively the filling system can be integrated into a Hosokawa Downflow booth or Hosokawa Glovebox/Isolator system.
- All of our systems are available in bespoke designs suitable to meet customers’ requirements for the application.
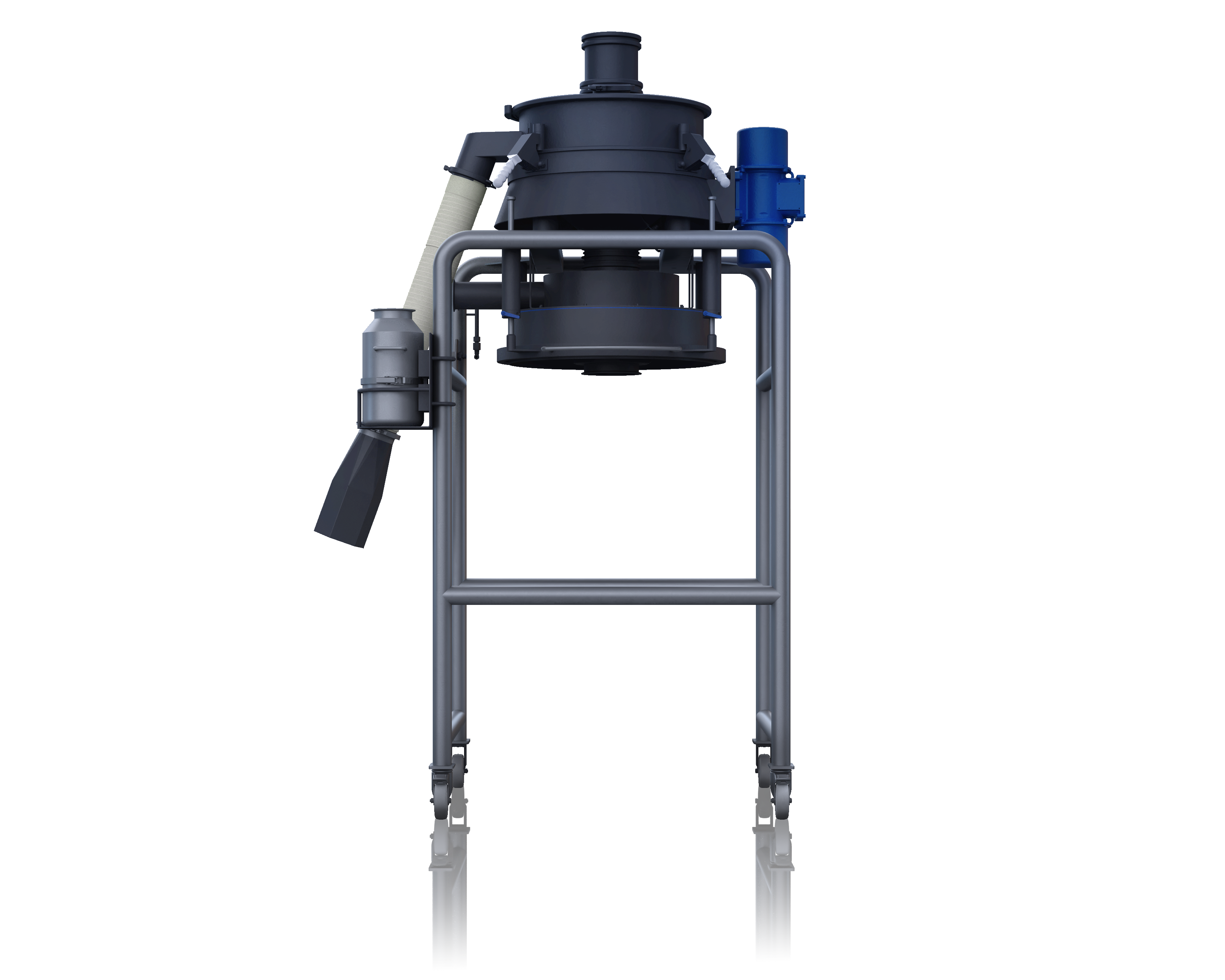
Packing Heads
Packing heads are an integral part of our filling and weighing systems and are used in various process steps in the production of lithium-ion batteries. On’s pack-off solutions are hardwearing, energy-efficient, easy to use and simple to maintain to make your battery production as efficient as possible.
Applications
- Packing of various raw and active materials in the production of lithium-ion batteries
Types of packing heads
Inward inflatable packing head seals the liner to the packing head on the outside of the liner sealing it onto the outside of the packing head and ensuring the seal does not come into contact with the product. There is no contact between the seal and the product meaning the seal stays clean and is easy to wipe clean. Quick product change overs as there is no contamination on the seal from previous products.
- Containment level is high.
- Product contact is none.
- Can be used with Single or Continuous liners
Outward inflatable packing head seals the liner to the packing head on the inside of the liner on the end of the packing chute, inflating like a tire. Only the very bottom of the natural rubber seal comes into contact with the product. There is minimal contact between the seal and the product meaning the seal stays largely clean and is easy to wipe clean. Product change overs require a quick wipe clean of the seal to ensure no residual contamination from previous products.
- Containment level is high.
- Product contact is minimal.
- Can be used with Single or Continuous liners
Downward sealing head – available in both inflatable and solid seal configurations. Typically used for sealing onto drums, intermediate bulk containers (IBC), bottles, the downward sealing head can be movable on cylinders or gas struts if required, to lower the head into the correct place to ensure correct containment of the container to be filled. Inflatable sealing heads provide even greater adjustment to ensure a perfect seal even with older, slightly damaged IBC’s.
- Containment level is high during filling.
- Containment level overall is medium as container is briefly open during changeover of containers to be filled.
- Can be used with drums both with and without liners.
O-ring canister packing head – simplest solution available, liner of drum or neck of FIBC sealed to the outside of the packing head by O-ring(s). O-ring provides seal during filling of the container/liner.
- Containment level is high.
- Product contact is minimal.
- Can be used with Single or Continuous liners
Your advantages with our packing heads
- Packing head system with single liners for a fast cycle time solution
- Packing head system with continuous liners prevents powder exposure to the local environment / operators.
- Packing head system with downward sealer for high volume discharge.
- Packing systems can come with combinations for filling FIBC/drum, IBC/drum and FIBC/IBC allows a flexible approach for diverse product duties.
- Safe change O-ring system limits or excludes powder exposure to the environment
- Packing head systems can be supplied with the following Hosokawa equipment for secondary or increased containment levels: Horizontal Laminar flow Booth, Downflow Booth or enclosed within one of our Glovebox/isolator systems for containment down to OEB5/6
- All our packing head systems can have built-in purge and exhaust of the filling head or be run under Air or an inert medium i.e. nitrogen purged. Built-in weighing system for real time weight display during filling possible as well as filling to a chosen set weight and vibration tables for powders that peak during filling
- Packing systems are available with ATEX, Control systems that can be stand-alone, PLC, integrated into Customer’s DCS site wide control systems, part of a SCADA system.
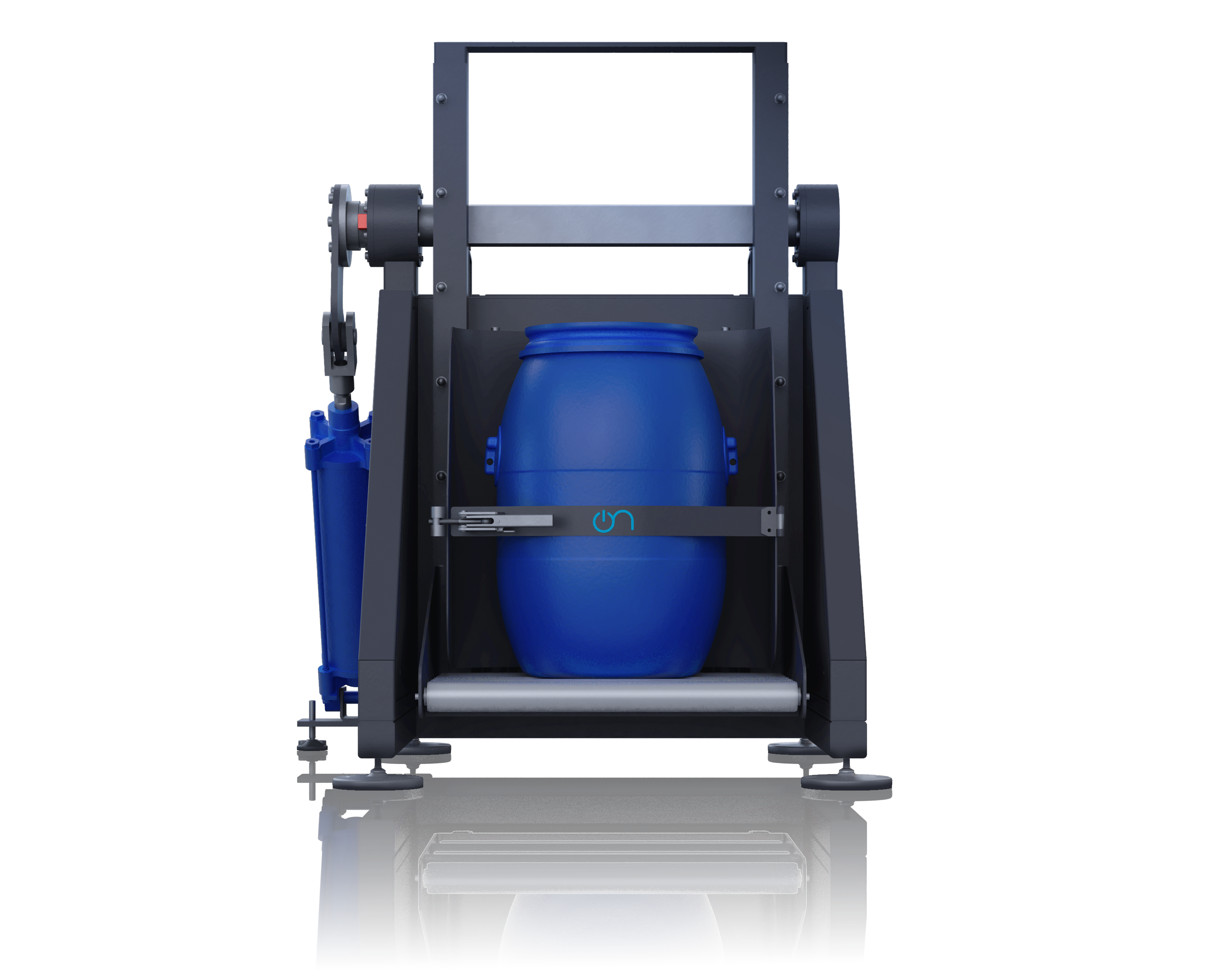
Drum Tippers
Drum handling equipment is used for safely introducing bulk raw material, including hazardous powder, into a process system, which may have a complex high containment element. Drum tippers are designed to minimise the amount of manual handling of the product
Applications
- Feeding raw and active cathode and anode materials into a process system
- Drums that contain hazardous substances pose several risks. Drums are often heavy and difficult to move while the contents may be harmful or even flammable. This means, under COSHH regulations, having the correct procedures and provisions for their handling are vital.
Principle of operation
Our drum tippers are tailored specifically for optimal performance and integration into our containment solutions, which can include everything from Downflow Booths, Gloveboxes and Isolators, to complex systems for the production of lithium-ion batteries.
Customizable drum tippers, manual or powered and ATEX certified models are available for customers’ specific needs.
Our automated drum tippers incorporate interlocked safety cages to ensure compliance to CE, UKCA and PUWER regulations, as well as multi-chamber isolators with integrated automatic drum tipping to meet maximum OEL requirements and provide complete product protection.
Your advantages with our drum tippers
- Glovebox with drum tipper: robust design at lower cost for containment and transfer of materials from drums into the glovebox
- Adherence to Good Manufacturing Practice (GMP)
- Electric, Pneumatic tippers, Hydraulic mechanical tippers available
- Tailor-made for integration into all Hosokawa Micron containment equipment
- ATEX rated versions available (Zone 1/21 and Zone 2/22)
- All of our solutions are supplied in stainless steel as standard, with a further option for powder-coated carbon steel, if required