Advanced graphite for your lithium-ion battery production
The anode of a battery consists of an approx. 8 - 18 µm thick copper foil, which is coated with active material (graphite) and various additives.
Graphite is therefore the most important battery anode material in the production of lithium-ion batteries. The black, platelet-shaped mineral is widely sourced and brings a number of numerous advantages for the manufacturer. After coating, the tap density of graphite is relatively high and the electro-chemical performance is relatively stable. Additionally, the actual specific capacity density can be close to the theoretical specific capacity. However, graphite also carries several disadvantages as a battery anode material. Most of all, its capacity to meet the actual demand is insufficient - a demand that is expected to increase rapidly in the next years, mainly driven by the growing number of electric vehicles.
To meet the demand for graphite in the long term, the graphite in battery production must be processed with as little loss as possible. In this way, the graphite can be used as effectively as possible. In addition, the characteristics of the graphite must be advanced in order to increase the performance of the battery. The particle size plays a role here because it determines how quickly the battery can be charged and discharged. At the same time, the tap density determines the energy density, i.e. the distribution of the graphite on the surface of the anode copper foil. The specific surface area also influences the capacity of the battery after the first charge.
To achieve the optimum battery performance results, ON has developed technologies for advancing both natural and synthetic graphite.
Natural and synthetic graphite
There are two kinds of graphite used in the production of lithium-ion batteries: natural and synthetic or artificial graphite. Natural graphite is sourced directly from graphite mines. As it is a natural raw material, there are always impurities, and the relatively soft graphite can be compromised by the surrounding hard mountain material. As these impurities make natural graphite more abrasive than its synthetic counterpart, the machines used in processing are subject to wear.
For the end product, in addition to a high yield, customers wish for a steep particle size distribution and a high tap density. At the same time, the top cut must also be adjusted, and the specific surface area should be very low (low BET values). A high product quality later increases the capacity of the batteries.
Synthetic graphite on the other hand is made by graphitising petroleum coke or needle coke. It is relatively pure, and its mechanical characteristics can be specifically influenced and optimised by the production process. Artificial graphite is usually not explosive and abrasive. However, it can contain metal impurities that are magnetic and should be separated after the pre-grinding process. Apart from product quality, high yields and low specific energy consumption are particularly important for customers.
In most cases¸ a mix of natural and synthetic graphite is used in the production of battery anode material.
Feed material and rounded graphite: SEM images (synthetic graphite)
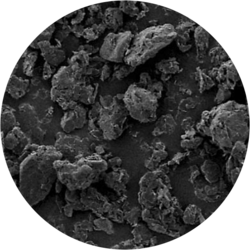
Feed material synthetic graphite:
Tap density 600 g/L
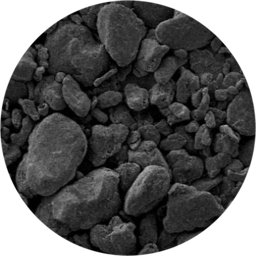
Rounded synthetic graphite:
Tap density 1000 g/L
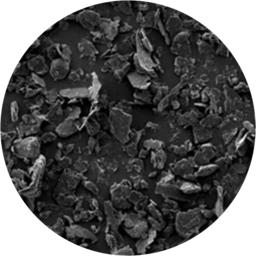
Feed material natural graphite:
Tap density 426 g/L
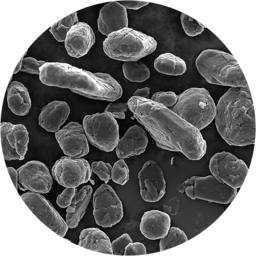
Rounded natural graphite:
Tap density 920 g/L
Graphite optimization technology for high-performance anode material
To obtain high performance battery anode material and to make optimal use of the raw material it is necessary to adapt the graphite to the requirements of the application and to process it accordingly. The main focus here is on high product quality, which in turn provides the best possible battery performance. Furthermore, the appropriate graphite technology should also achieve the highest possible yield. At the same time, the specific energy consumption should remain as low as possible. Flexible product parameters and individual settings on the graphite processing plants from ON also guarantee that customers receive a product that meets their specific requirements.
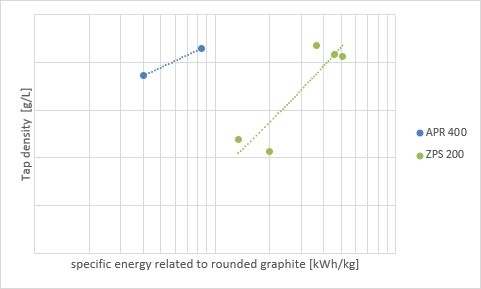
Individually configured graphite processing plants
Every customer is different. That's why we develop our machines and systems specifically for each customer. The combined expertise of the entire Hosokawa Micron Group, which stands behind ON, helps us to achieve this. Our graphite technologies are perfectly coordinated and interlock smoothly. In addition, trials with customer products can be carried out in our test centres in Augsburg and Doetinchem in order to develop the appropriate process. For our customers, this means that they obtain a product that exactly meets their requirements and a graphite processing system that was developed specifically for them.
Graphite processing and graphite spheroidization
The processing of graphite consists of four steps
Pre-grinding, fine grinding, spheroidization and dedusting and mixing/coating coated with binders and carbon black.
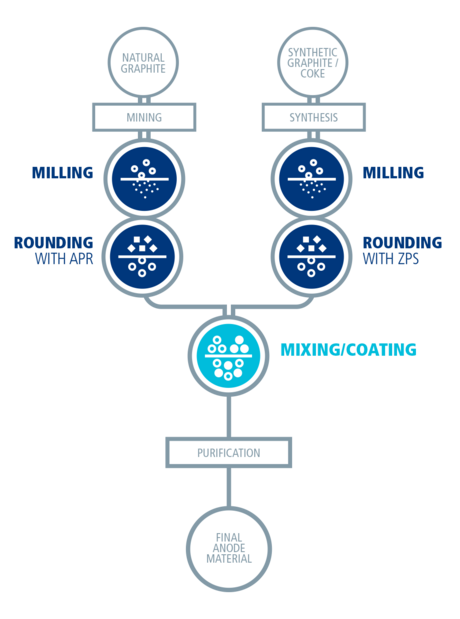
Pre-milling
Pre-milling can be carried out with different types of mills. Which mill is suitable depends on the feed material and the feed size. Possible solutions include a fine impact mill (e.g. Ultraplex UPZ) or a classifier mill (e.g. Zirkoplex ZPS). Natural graphite can usually be processed without pre-grinding.
Fine milling
This process is the same for both synthetic and natural graphite. It is a continuous process and determines the top cut of the graphite.
Graphite spheroidization and dedusting
Different graphite machines and processes are required here for natural and synthetic graphite. The particle size distribution is adjustable. Both spheroidization and dedusting are batch operations.
Mixing/Coating
When a mix of natural and synthetic graphite is used, the specific characteristics of both raw materials need to be combined. This can be achieved by homogenizing these compounds in a mixer. High shear mixers also form a strong coating of other materials, such as carbon black and binders around the rounded graphite particles.
Why do the platelet-shaped graphite particles have to be rounded or spheroidized?
The roundness of graphite brings numerous advantages. On the one hand, it increases the tap density, and thus ensures a better volumetric storage capacity of the battery anode. On the other hand, the graphite rounding improves the intercalation kinetics so that the battery anode can be charged more quickly. In addition, the battery becomes more durable, and the cycle stability is increased.
Apart from these advantages for the performance of lithium-ion batteries, ON's process has other plus points: Since fewer machines are needed here than for conventional processes, customers save space. Furthermore, the effort for maintenance and service as well as the energy costs are reduced.
Machines for enhancing graphite
ON offers various machines for enhancing graphite. Which graphite machine is suitable depends on whether natural graphite or synthetic graphite is processed.
For pre-milling natural graphite, a fine impact mill like UPZ or a classifier mill like ZPS is recommended. Fine grinding is usually carried out with a classifier mill like ZPS or ACM.
The graphite spheroidization is carried out by means of the Alpine Particle Rounder APR with downstream classifying. As an alternative the classifier mill ZPS can also be used for rounding. However, this solution requires much more energy and space.
With synthetic graphite, the UPZ fine impact mill is generally used for pre-milling. For grinding, the ZPS or ACM classifier mills are recommended. As artificial graphite is usually already much more spherical after grinding, it requires less energy for spheroidization. Here, the classifier mill ZPS can also be used to round the graphite in batches with integrated classifying. As alternatives, the TTD or ATP air classifiers can be used for dedusting. Depending on the requirement, the shaping step can be left out. Both kinds of graphite can be mixed and coated with the Nauta and Cyclomix mixers, for coating the Nobilta is recommended.
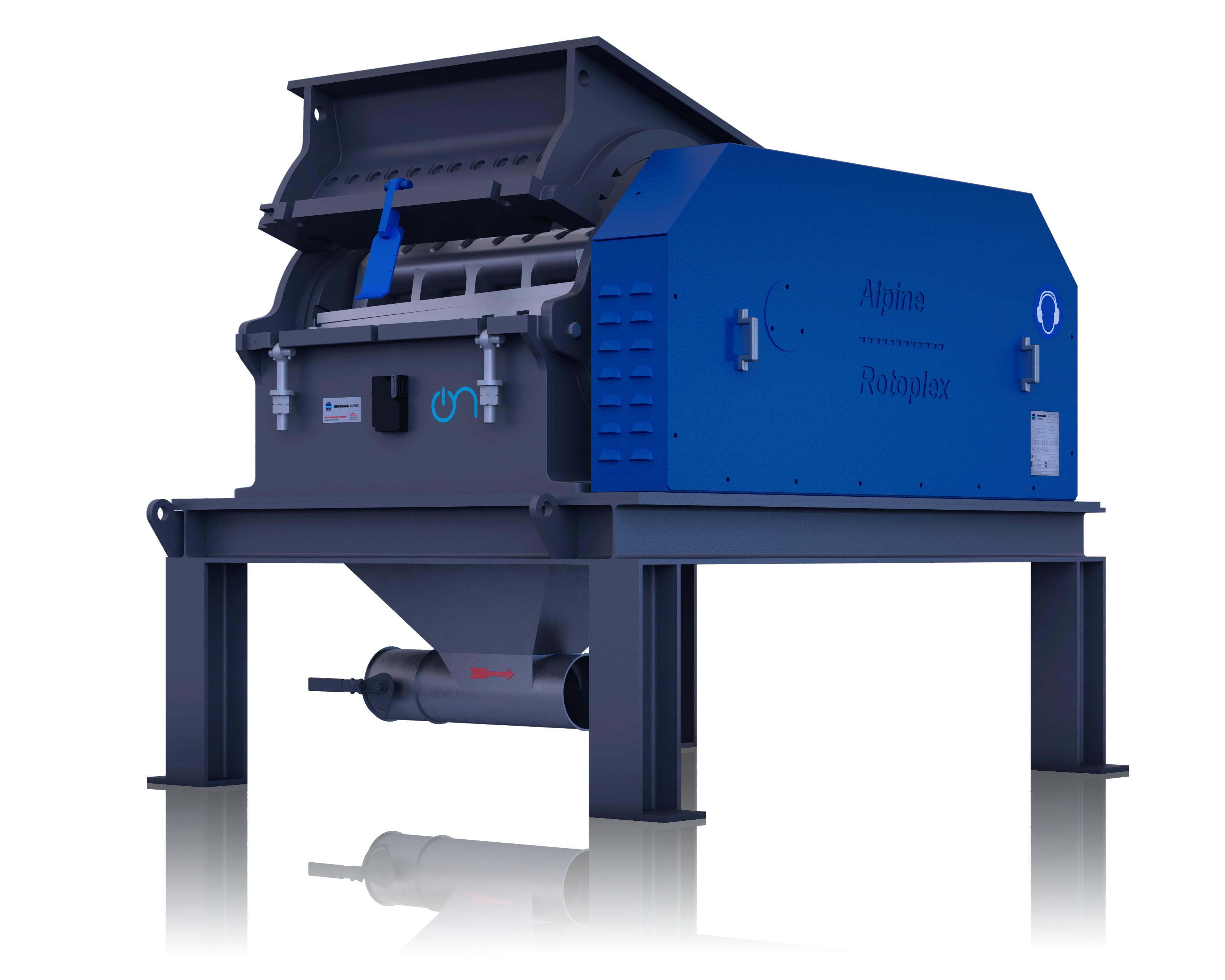
Rotoplex Cutting Mill
The Rotoplex granulator is a real classic in our range of machines and is upgraded continually to accommodate the latest technology. In the production of lithium-ion batteries, it can be used for a variety of tasks -from pre-crushing graphite for the battery anode to various recycling tasks. The Rotoplex is an efficient all-in-one solution that achieves high yields and recycling rates thus ensuring minimal product waste.
Applications
- Anode materials: graphite, copper
- Cathode materials: aluminium foil
- Recycling: cutting cathode and anode in preparation for the separation of the black mass, pre-crushing for further processing with the UPZ fine impact mill or the AFG fluidised bed opposed jet mill
Principle of operation
The Rotoplex cutting mill is characterised by an extremely powerful and robust design, incorporating the unique cross-scissor cut rotor. The rotor guarantees optimal material distribution, a sharp cut and a low-dust product at maximum cutting performance. A housing made of fracture-resistant cast iron ensures that even in heavy continuous use, Rotoplex granulators do their job reliably over many years.
Your advantages with the Rotoplex cutting mill
- Unique cross-scissor cut rotor for energy-efficient cutting, no residues of copper and aluminium, homogeneous distribution of foil flakes without small parts
- Even distribution of the product
- Knives can be replaced individually in segments for easier maintenance and cleaning. This also reduces maintenance costs and the cost of spare parts
- Assurance of good separability of black mass and foil
- Possibility of introducing an inert gas to protect the material and prevent combustion (ATEX)
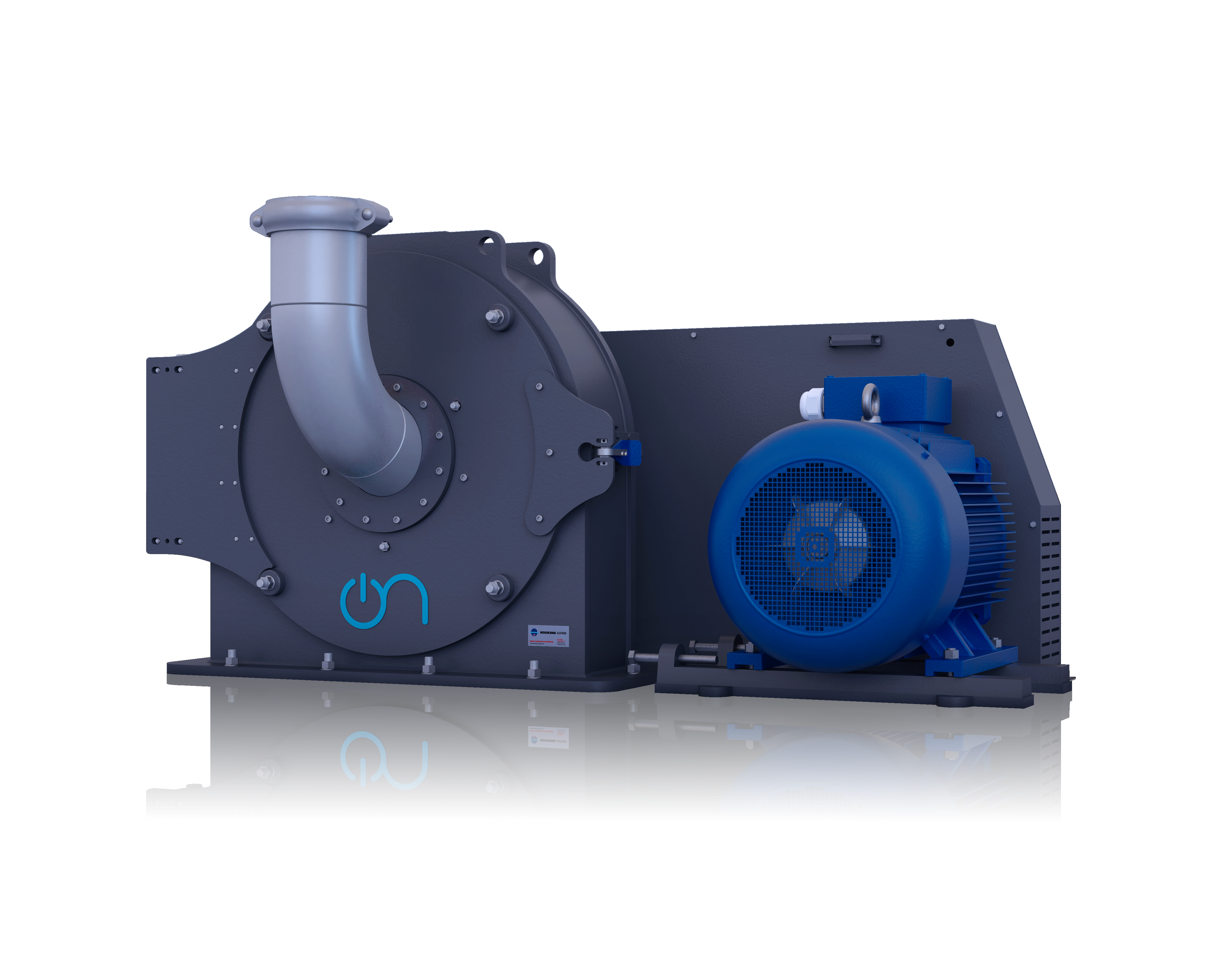
Ultraplex UPZ Fine Impact Mill
The Ultraplex UPZ fine impact mill is a versatile size-reduction system with exchangeable grinding elements. Possibilities include beater disc, pin discs, swing beaters and plate beaters, sieves and grinding tracks. Depending on the grinding element, finenesses between 50 µm to approx. 5 mm can be achieved. Which grinding element you choose for pre-milling synthetic graphite depends on the feed size. For direct scrap recycling of production scrap plate beaters are recommended.
Application
- Pre-milling of synthetic graphite: pre-process before grinding with ZPS classifier mill for graphite pieces larger than 4 cm
- Standard recycling solution for delamination to separate cathode material from aluminium foil
Principle of operation
UPZ fine impact mills are universal in operation for the size reduction of soft materials up to 3 on the mohs scale. The product is fed centrally via the mill door. The machine housing is designed to accommodate all the different milling elements. The fineness is adjusted by selection of the corresponding size reduction elements and as a function of the machine speed; the belt pulley needs to be exchanged when a larger machine size is being selected. If the mill is used for direct recycling of production scrap, downstream classifying is necessary.
Your advantages with the UPZ fine impact mill
Pre-milling of synthetic graphite:
- Relatively small size: saves space
- High throughputs
- Energy-saving grinding process: pre-milling reduces energy consumption during the grinding process with the ZPS classifier mill
- Less wear and tear on the ZPS classifier mill
Direct recycling of production scrap:
- High degree of separation
- High throughput
- Continuous and simple process
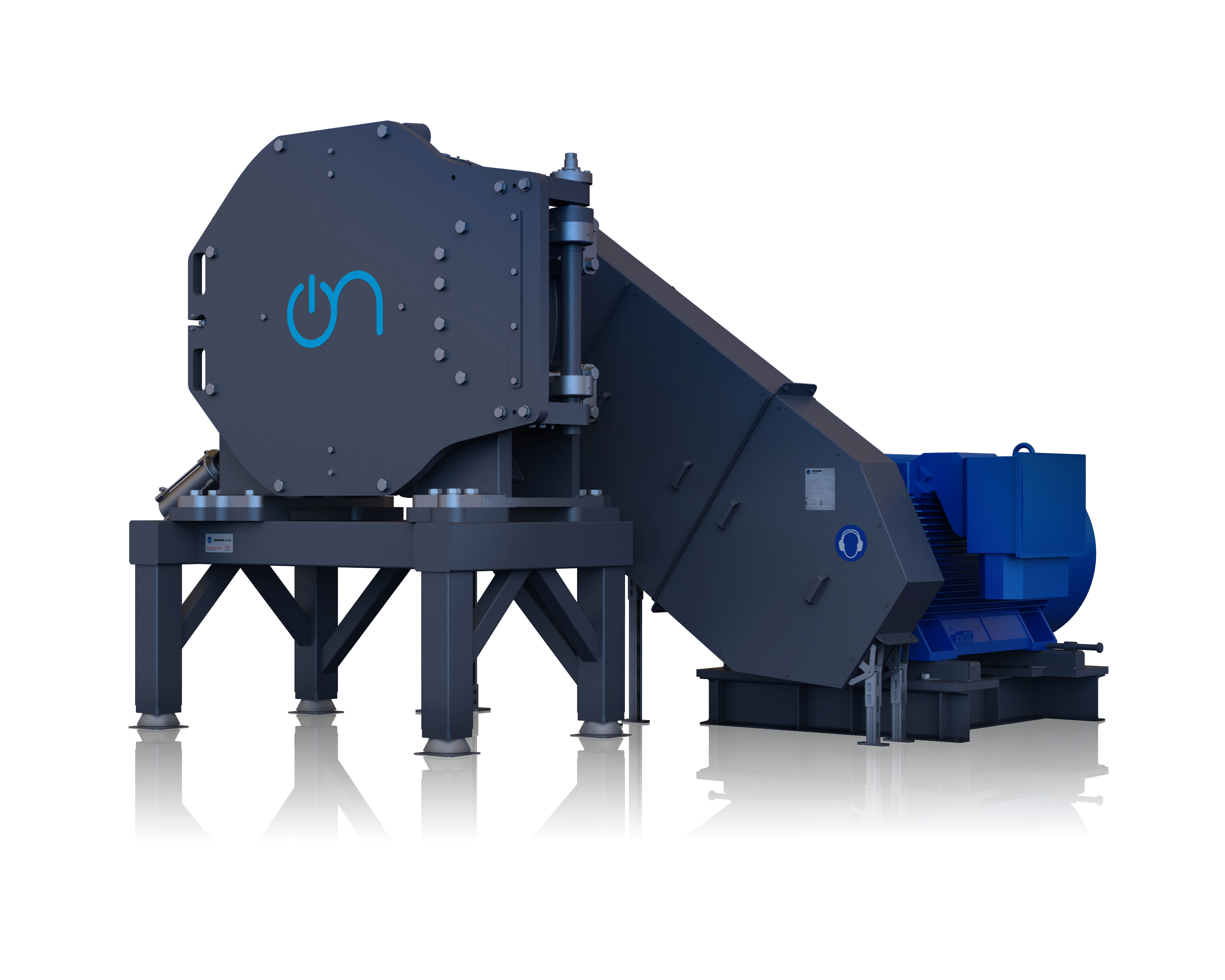
APR Particler Rounder
The Alpine Particle Rounder APR was specifically developed for the spheroidization of natural graphite. This is a completely new process that allows the graphite to be used more efficiently. The closed system runs batchwise and rounds the plate-shaped graphite in just three minutes.
Application
- Natural graphite
Principle of operation
After pre-crushing in a classifier mill, the graphite is filled into the process chamber in batches via loss and weight system and stressed for the necessary time. The stress is caused by overlapping impact stress between graphite particles and rotor beaters and from a frictional or shear stress between the graphite particles with the housing wall. Depending on the requirements, batch size, rotor speed and rounding time can be varied. Once the rounding process is complete, the graphite is discharged from the machine via a discharge opening.
After the graphite has been rounded in the APR, it is dedusted in a downstream, continuously operated air classifier. This separates the fine material that is produced during rounding. However, the APR does not have an integrated classifier. Our TTD air classifier is recommended here - one air classifier can serve nine APRs.
Your advantages with the Alpine Particle Rounder APR
- Simpler set-up with fewer machines than other graphite spheroidization systems. This saves space and reduces maintenance and investment costs.
- Energy-efficient, as fewer machines are required and no air flow or fan is necessary
- Short process times
- Flexible use for all common finenesses of rounded natural graphite from x50 = 10-12 µm to x50 = 20-25 µm
- Less product loss during the rounding process: yields of up to 80 %
- Very high tap density compared to other solutions. This reduces the surface area (BET) of the battery and increases the storage capacity, the fast-charging capability and the service life of the battery.
- Fine particle size distribution: This increases the capacity of the lithium-ion batteries
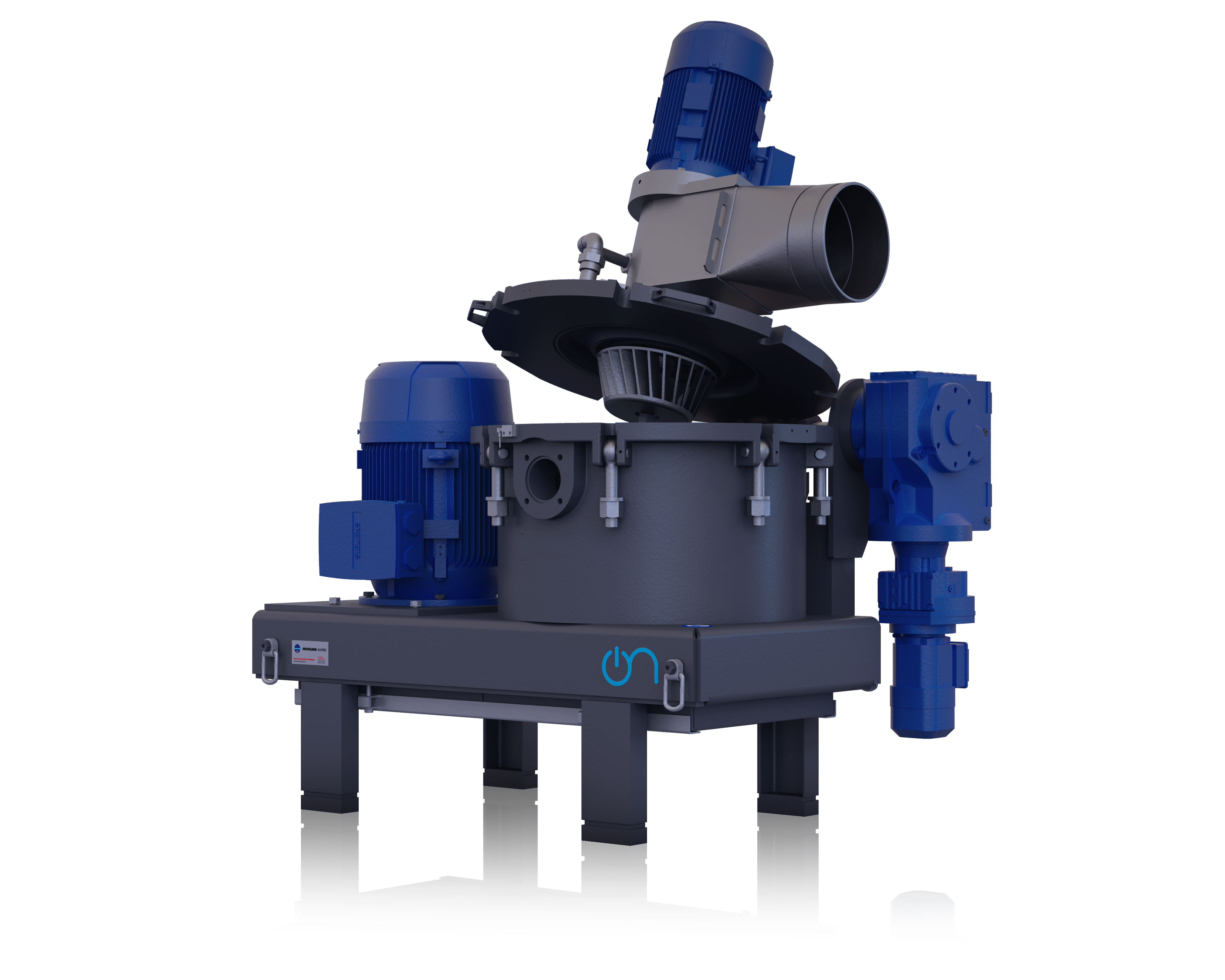
ACM-BC Classifier Mill
The ACM-BC is a fine impact mill with a built-in classifier. It was specially developed to grind and classify materials that must not suffer any metal contamination, which is the case with cathode materials for the production of lithium-ion batteries. This is why all machine parts that come in contact with the powder are made of ceramics. The mill and classifier structure is thoroughly simplified, resulting in high reliability and significant reduction in operating costs.
When grinding raw and active materials for the cathode, synthesized cobalt-based materials have a tendency to become larger in particle size due to the neck growth between particles. Therefore, efficient turnover of the lithium ions from the inside of the particle becomes difficult. As a result,. the packing ratio decreases when the aluminium foil of the electrical current collector is coated with the lithium compounds and the coated surface becomes uneven. Ultrafine particles can also cause handling problems due to their adhesive and cohesive nature. This is why fine grinding of the raw and active materials is necessary.
Applications
- Grinding and classifying of lithium compounds: LCO, NCM, NCA, etc.
Principle of operation
The product is pneumatically fed into the ACM classifier mill. Size reduction is achieved by the impact of the product on the rotating grinding elements and against the stationary liner. The cooling, conveying and classifying air sucked through the mill by the downstream fan captures the product and guides it along the guide vanes of the vane ring.
A characteristic feature of the ACM is the integrated dynamic classifier. The product-air mixture is evenly fed by the guide vanes to the rotating classifier. Because of the two opposing forces and the different masses of the particles, the product is separated in the classifying zone into a coarse fraction and a fine fraction. The coarse material is rejected by the classifying wheel and returned to the grinding zone for further comminution. The fine material passes the classifying wheel and exits the grinding chamber. The cut point is set via the speed of the classifying wheel, which can be adjusted continuously even during operation.
Your advantages with the ACM-BC classifier mill
- Grinding and classifying operation in one machine
- Cost reduction due to simplified mill and classifier structure
- Contamination-free product
- Ceramics parts to reduce risk of fire as there is no wear or metal contamination of the product
- Steep particle size distribution
- Sharp and easily adjustable precision of cut
- Easy cleaning and maintenance
- Low specific energy consumption

Mikro ACM Classifier Mill
The Mikro ACM® Air Classifying Mill is a fine mechanical impact mill with an integrated classifier. It was designed to grind a wide range of materials down to D97 < 20 µm. In the production of lithium-ion batteries, it is used for grinding and micronizing both cathode and anode materials.
Applications
- Grinding of lithium carbonate
- Grinding of coke
- Micronizing of graphite
Principle of operation
The product is pneumatically fed into the Mikro ACM® Air Classifying Mill. Size reduction is achieved by the impact of the product on the rotating grinding elements and against the stationary liner. The grinding zone is coupled with an internal dynamic classifier which controls the end-product particle size via recirculating the coarse particles back into the grinding zone. These particles are recirculated through the grinding and classification zones until fine enough to pass through the classifier, and captured downstream via cyclone or filter. The cut point is set via the speed of the classifying wheel and the airflow, which can be adjusted continuously even during operation.
Your advantages with the Mikro ACM® Air Classifying Mill
- Consistent/tight particle size
- Excellent top size control by use of integral, internal classification
- Durability and reliability due to robust construction
- Wear-protected to minimize contamination of the product
- Available in multiple sizes
- Low operating costs

Zirkoplex ZPS Classifier Mill
The ZPS Zirkoplex classifier mill has been tried and tested in practical application all over the world. The design and capacity are constantly updated to adhere to the latest research results and to meet practical requirements. In lithium-ion battery production it can be used for a variety of tasks including the spheroidization of synthetic graphite.
Applications
- Pre-milling of natural graphite and petroleum coke
- Spheroidization of synthetic graphite
- Grinding and spheroidization of petroleum coke
Principle of operation
The size-reduction elements of the Zirkoplex ZPS consist of an impact beater unit plus a stationary triangular-ribbed grinding track that surrounds the grinding chamber. The impact beater unit has been designed to achieve very gentle and energy-efficient grinding. The impact beaters are exchangeable; the grinding track is in segmented design. A Turboplex ultrafine classifier with one or more horizontal classifying wheels is integrated into the top section of the mill.
The material introduced via a metering device at the feed spout is caught by the impact beaters of the beater disc. The combined action of the beaters and grinding track serves to comminute the product, which is then transported via the classifier to the fines discharge. The air introduced into the machine at the air inlet cools, transports and also classifies the product in the integrated classifier. The fines, extracted in accordance with the cut point set at the classifier, exit the machine via the fines discharge. The end product must be separated from the air in a downstream system-sided collection unit.
Particles that are too coarse are rejected by the classifying wheel and are comminuted by the beater unit until they can pass through the classifying wheel and thus correspond to the required fineness as specified by the classifying wheel speed.
The spheroidization process takes place after grinding. The graphite or petroleum coke is rounded in batches with integrated classifying. The operation is carried out via a cyclone dust collector. For additional dedusting after the spheroidization process, the TTD air classifier is recommended.
Your advantages with the ZPS classifier mill
- Sharp separation and steep particle size distribution
- Different target finenesses possible (d50 = 10 – 12 μm; d50 = 15 – 16 μm; d50 = 18 – 22 μm)
- High throughputs (grinding): Product trials with petroleum coke have shown a throughput of 2–3 t/hour
- Yields of up to 90%
- Fast spheroidization of petroleum coke with little loss of material
- High tap densities possible for higher storage capacity of the batteries
- Low BET values
- Flexible settings, quick adjustment of product parameters
- Low specific energy consumption
- Pressure shock resistant version up to 10 bar possible (graphite) and compliance with ATEX regulations: This makes the ZPS classifier mill suitable for many different products and protects staff and production environment
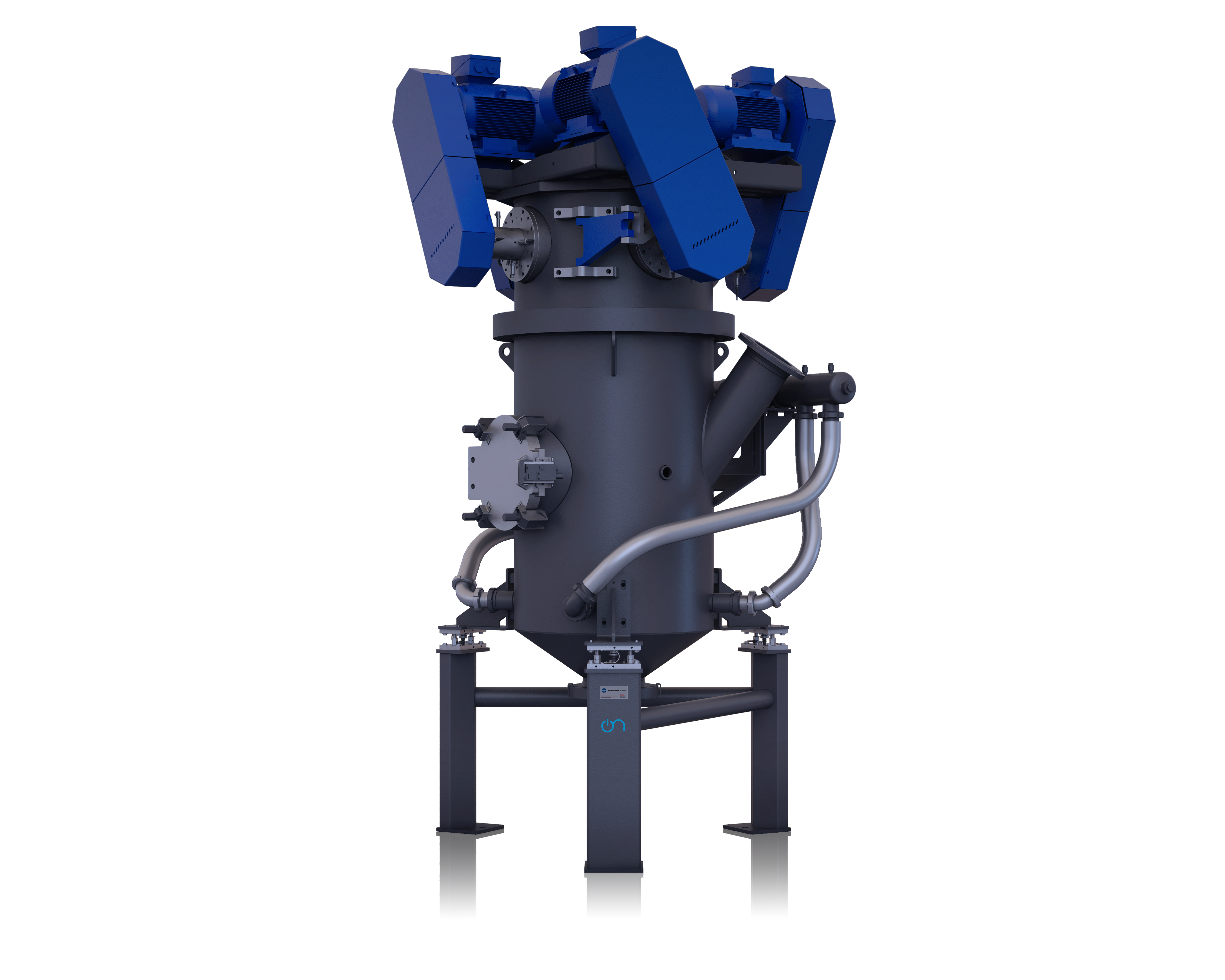
AFG Fluidised Bed Opposed Jet Mill
The AFG fluidised bed opposed jet mill is used in various process steps during battery manufacturing. It is used for the production of powders with a steep particle size distribution and sharp top size limitation in the range < 5 µm to 200 µm.
Applications
- Grinding of lithium and lithium compounds
- Grinding of silicon and silicon compounds
- Grinding of rare earths (with highly flammable properties)
- Delamination: separation of cathode material from aluminium foil or anode material from copper foil
Principle of operation
Jet mills are impact mills which are used to achieve maximum fineness values at maximum product purity. Such particle sizes can only be achieved in connection with an air classification process step . Fluidised bed opposed jet mills are equipped with a dynamic deflector-wheel classifier.
In a fluidised bed opposed jet mill, the product is fed via a feed lock. A product fluidised bed then forms in the grinding chamber, which is fluidised by the gas jets. From there, the particles enter the gas jets and are accelerated. They collide with each other again and again and are thus comminuted. A classifier wheel rejects those particles that are still too large and conveys them back into the fluidised bed. The particles that are fine enough are separated from the grinding gas by a separator or dust filter.
The fineness of the product is adjusted via the speed of the classifier wheel. All-important is a high product loading of the nozzle jets in order to obtain a high particle concentration and thus high impact probabilities. The unique Megajet nozzles were specifically developed for this purpose. The product level in the machine is controlled by load cells or by monitoring the current loading of the classifier drive.
Your advantages with the AFG fluidised bed opposed jet mill
Production of active cathode and anode materials
- Wear protection with different ceramics (standard for grinding lithium, optional for grinding silicon and rare earths) : no contamination of the product. In addition, the effort for maintenance and service is reduced and thus also the downtimes.
- Easy accessibility for easy cleaning and maintenance
- High throughputs with low pressures: energy-efficient production of fine powders with little energy
- Design for contamination-free processing
- Gas- and dust-proof design protects staff and the work environment from toxic lithium compounds and protects the materials from exposure to moisture
- Integrated classifying wheel(s) arranged horizontally in the classifier top section. The results are a steep particle distribution and an exact top cut. These are necessary for optimum coating thicknesses for electrodes.
- When processing silicon and silicon compounds, the system can be run with nitrogen or argon. This reduces costs. Due to the lack of oxygen, the silicon cannot oxidize. This makes it more active and requires less space in the anode. It also makes it possible to process rare earths.
Direct recycling of production scrap
- High degree of separation prevents loss of valuable raw materials. The cathode or anode material is very pure and contains no traces of aluminium or copper foil.
- Separation from the foil takes place in the cyclone: no additional classifying necessary
- Gas- and dust-proof design protects the materials from moisture
- If the system has to be operated with nitrogen it can be run in a closed loop. This keeps the loss of nitrogen low and reduces costs.
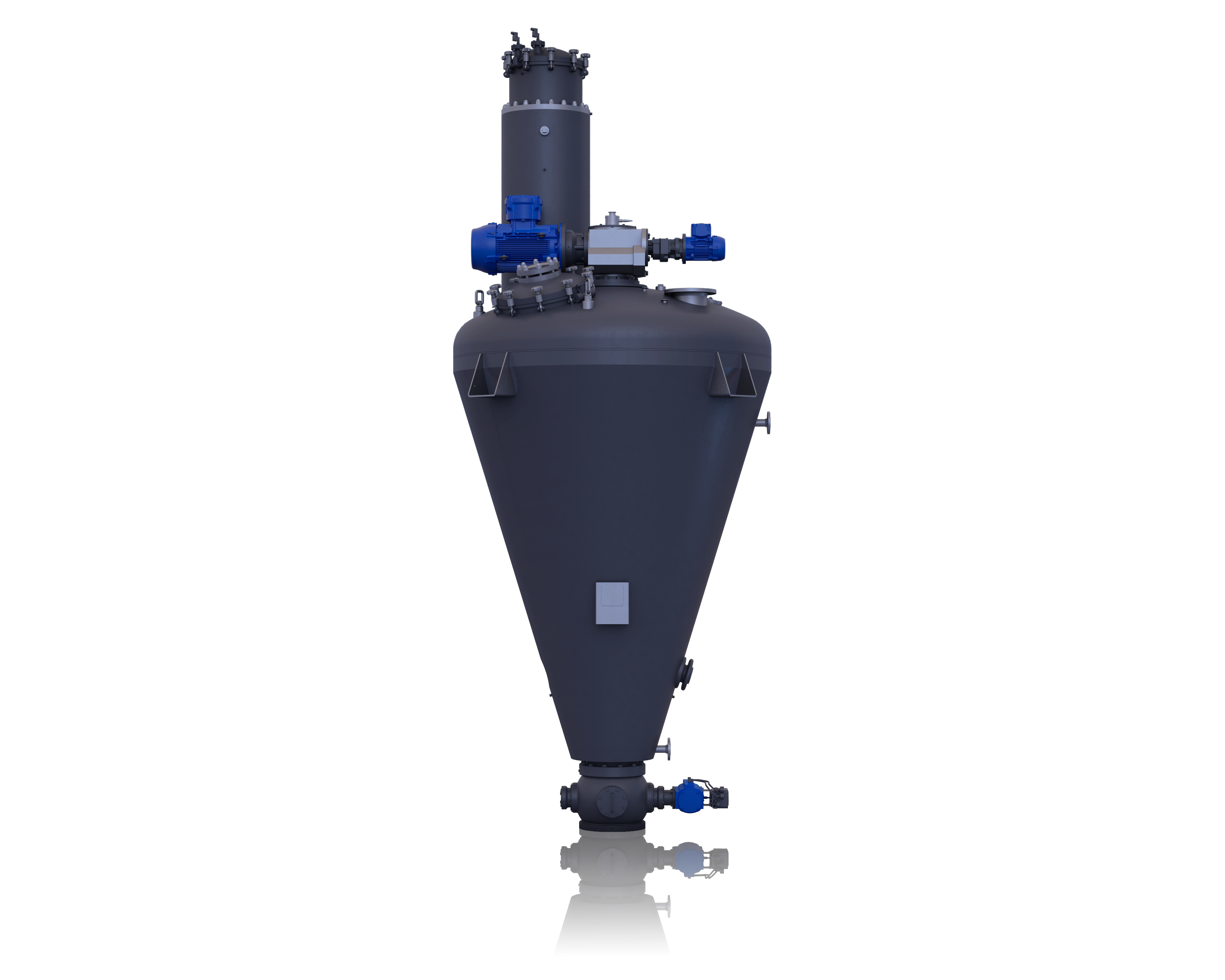
Nauta Conical Screw Dryer
The Nauta conical screw dryer is a vacuum dryer for low shear mixing and drying that is suitable for drying powders, granules, pastes and viscous slurries. It can also handle toxic or explosive products, such as lithium, an important raw material in the cathode of a lithium-ion battery.
The Nauta conical screw dryer provides gentle mixing and drying which results in a homogenous mixture without product distortion. This is essential for an optimal battery performance.
Applications
- Drying of lithium
- Cathode Active Materials
Principle of operation
The Nauta conical screw dryer is a conductive dryer with high drying efficiency. The rotating cantilevered (free hanging) mixing screw, conveys the product from the bottom of the vessel to the product surface. The thermal energy required for the drying process is transferred to the product via a heated jacket, which can be heated by various media such as steam, hot oil and water. The jacket ensures rapid distribution of heat into the product in combination with efficient mixing.
The vacuum inside the dryer allows vapours to be removed at low temperatures, which makes the Nauta® vacuum dryer ideal for drying heat-sensitive products. The vapours are removed through a dust filter fitted on top of the vessel. This prevents the dust from entering the vacuum system.
Your advantages with the Nauta conical screw dryer
- Cantilevered mixing screw for easy discharge and low maintenance: As there are no bearings and thus no lubricants in the products zone, contamination of the product is impossible.
- Full vacuum execution to achieve PPM levels of moisture: This results in a low level of end moisture and thus in a high quality of the end product.
- The Nauta® conical screw dryer has gentle agitation minimizing the effect of wear or contamination of your product.
- Bottom outlet for an easy, fast and full discharge of the dryer and easy cleaning of the machine. Therefore, a high yield is guaranteed.
- Containment: The Nauta conical screw dryer operates at full vacuum and promises a safe process. Operators and environment are protected, and the dryer is suitable for an ATEX environment. Furthermore, there is no contamination, and the raw materials are protected to prevent reactions.
- Scalability: The Nauta® conical screw dryer can also process large batch sizes. This makes the process reproducible; the dryer is available to handle volumes from 5 up to 30,000 litres. The result is a consistent product quality from small scale to production scale.

Cyclomix High Shear Impact Mixer
The Cyclomix high shear impact mixer combines high shear and impact mixing in one single machine. The result is a high level of homogeneity in the end product, meeting the stringent demands of the battery production industry.
By achieving homogenous mixing of cohesive powders in ultra-short cycle times, the Cyclomix ensures a full coating of binders and conductive additives around anode or cathode precursors. This process reduces the BET surface area, leading to enhanced battery performance.
With its consistent and high-quality mixing results, the Cyclomix high shear impact mixer is an indispensable tool for battery manufacturers seeking to optimize their production processes.
Applications
- NMC
- Natural graphite
- Synthetic graphite
- Lithium compounds
- LFP
- Nickel
- Cobalt
- Manganese
- CNT (carbon nanotubes)
- Silicon
- Lithium
- Carbon black
- PTFE
- PVDF
- Pitch
- Solid state
- Coating Neodium Iron boron
Principle of operation
The Cyclomix high shear impact mixer consists of a conical mixing vessel, equipped with a central paddle rotor, rotating at tip speeds of up to 30 m/s. The speed of the rotor creates centrifugal forces that push the product against the vessel wall, where the shape of the vessel causes an upward movement. The cover directs the product towards the centre of the mixer and at the top, an impact blade efficiently disperses cohesive powders and liquids.
Advantages of the Cyclomix high shear impact mixer
- Superior efficiency: The Cyclomix features a unique design where the shearing zone extends along the entire vessel wall, not just the bottom. This innovative feature makes the Cyclomix the most efficient high shear mixer available, achieving superior mixing and coating results with lower circumferential speeds and shorter mixing times compared to other mixers on the market.
- Central Paddle Rotor: Equipped with a central paddle rotor, the Cyclomix allows for easy product discharge and requires low maintenance. With no bearings or lubricants in the product zone, the risk of contamination is eliminated.
- Central bottom outlet: The central bottom outlet facilitates complete, easy, and fast discharge of the mixer, making it simple to clean and ensuring a high yield.
- Containment: The Cyclomix operates in an inert atmosphere and under/over pressure, protecting operators and the environment, and making it suitable for ATEX environments. This feature also ensures no contamination of the product, preserving the integrity of raw materials and preventing unwanted reactions.
- Scalability: The Cyclomix is fully scalable, allowing process settings to be reproduced consistently from 1 to 1000 litres of product. This guarantees constant product quality from small-scale to production-scale operations.
- Optional wear protection: Available wear protection options prevent equipment wear and further eliminate product contamination.
- Excellent temperature control: The Cyclomix offers superior temperature control, ensuring optimal product quality throughout the mixing process.
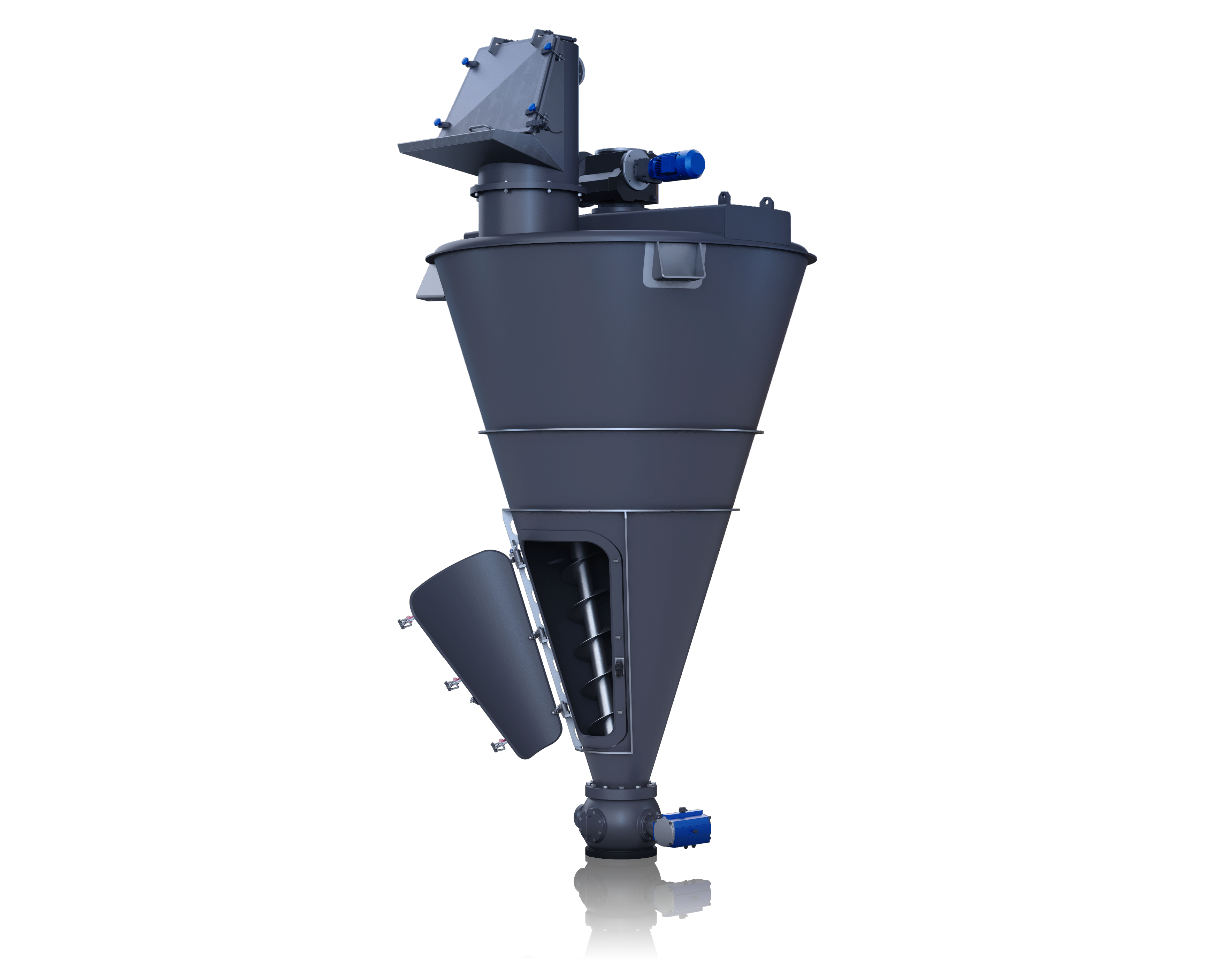
Nauta Conical Screw Mixer
The Nauta conical screw mixer is a batch mixer, specially designed for segregative, free-flowing powders and pastes. In battery production, it is often used as homogenizer. For instance, during production of anode material, specific characteristics of natural and synthetic graphite need to be combined. This can be achieved by homogenizing these compounds in a Nauta mixer. Furthermore, the Nauta® mixer may be used as an agitated feed hopper to create a consistent feed to the DMR flash dryer or various mills.
Applications
- Natural graphite
- Synthetic graphite
- Precursor (PCAM)
- Cathode Active Materials
Principle of operation
The Nauta conical screw mixer is a convective mixer with high mixing efficiency. It is gentle and guarantees maximum mixing accuracy without product distortion.
The rotating, cantilevered (free-hanging) mixing screw conveys the product from the bottom of the vessel to the product surface. The mixing screw is suspended from an orbital arm that rotates the mixing screw along the conical inner wall of the vessel, causing convective mixing of the particles and shear. The result of these simultaneous processes is fast and intensive mixing with low energy consumption and high mixing accuracy at the same time.
Your advantages with the Nauta® conical screw mixer
- Conical screw mixer for low shear mixing with low energy input: Free-flowing and segregative powders are gently mixed. The result is a homogeneous mixture without product distortion.
- Cantilevered mixing screw for low maintenance and easy discharge: As there are no bearings and thus no lubricants in the product zone, contamination of the product is impossible.
- Bottom outlet for an easy, fast and full discharge of the dryer and easy cleaning of the machine. Therefore, a high yield is guaranteed.
- Containment: The Nauta® conical screw mixer can operate at an inert atmosphere and at under/over pressure. Operators and environment are protected, and the mixer is suitable for an ATEX environment. Furthermore, there is no contamination, and the raw materials are protected to prevent chemical eactions .
- Scalability: The Nauta® conical screw mixer can also process large batch sizes. This makes the process reproducible; the mixer is available to handle volumes from 5 up to 100,000 litres. The result is a constant product quality from small scale to production scale.
- Versatility: The mixer can also be used as a feed hopper to create a constant feed for continuous dryers or mills.
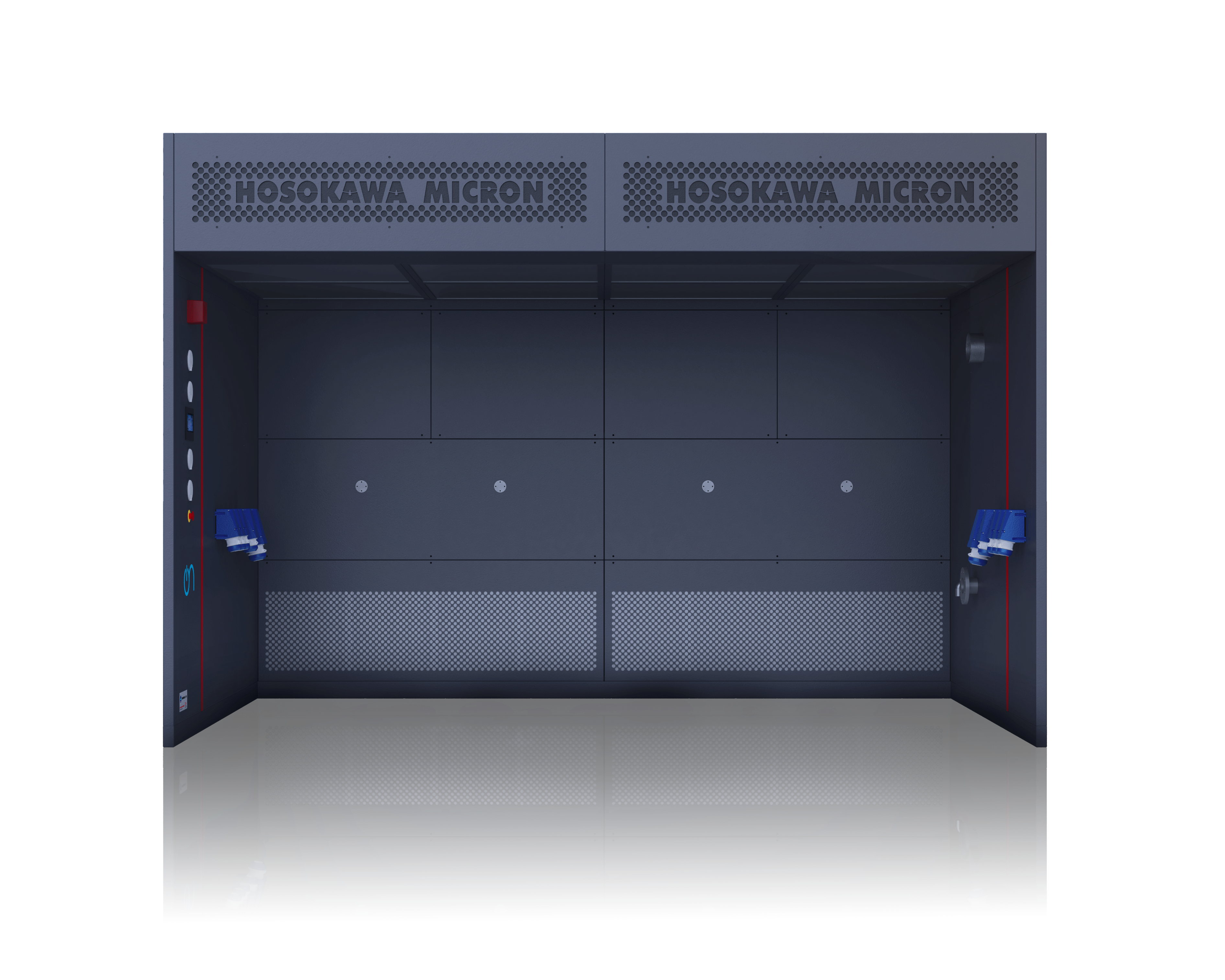
Downflow Booth
Downflow booths (single pass or recirculation) offer a pragmatic and ergonomic solution to containment requirements during the production of battery materials. Downflow Booths are used particularly where hazardous, toxic or sensitizing powders are handled, for sampling, weighing, sieving or conveying of powders, and containing individual process steps in an existing production line (factory) lay-out from lab scale to production scale.
Applications
- Containment of hazardous products during battery production
- Protection of personnel and product protection
Principle of operation
The air recirculation system ensures complete safety for personnel as a conditioned downflow of air passes vertically from the booth’s ceiling inlet plenum pushing any dust or vapours downwards and away from the operator’s breathing zone.
The air is extracted from the booth via low level grills mounted in the rear wall. The exhaust air is taken through a series of filters prior to recirculation into the booth.
Your advantages with the downflow booth
- Ergonomic access: The downflow booth is open fronted, this offers unrestricted operator access to the target operation (i.e. no physical impediment offered by the containment equipment).
- Flexibility to handle a large range of container types
- Capability to integrate additional process equipment
- It will allow clients to meet their safety needs without having to compromise on process efficiency.
- Multi-stage filtration with final HEPA grade
- Guaranteed operator exposure levels of <100 ug/m3: subject to good SOP
- ATEX design to meet standards and safety requirements
- Safe Change Filter Housings limit exposure of harmful products to the environment as potentially hazardous material is captured in filters that can be exchanged safely.
- Recirculation mode for handling powders and pharmaceuticals assures operator protection
- Single pass mode for hazardous products and solvent handling stops potentially harmful products coming into contact with operators
- Low noise due to improved fan selection and booth plenum design
- Controlled entry and exit airlocks to maintain air pressure control between adjoining rooms (generally with different air cleanliness standards)
- 5D High Containment Screens can meet client expectations for an even lower OEL. These are flexible and moveable screens which enforce physical separation between operator and material.
- Temperature cooling/heating packages to meet requirements for a certain ambient room temperature: The booth provides a constant temperature both for the operators and for products which require a defined ambient temperature.
- 70% energy savings, energy conservation mode of operation, LED lights, high efficient fan sets
- Modular design and plug & play system make for easy commissioning and fast installation and offers shorter lead times
- Easy cleaning saves time during production and reduces costs for operating staff. There is also less contamination from previous products being handled in the booth.
- Meets HSE standards and legal requirements to protect the operators
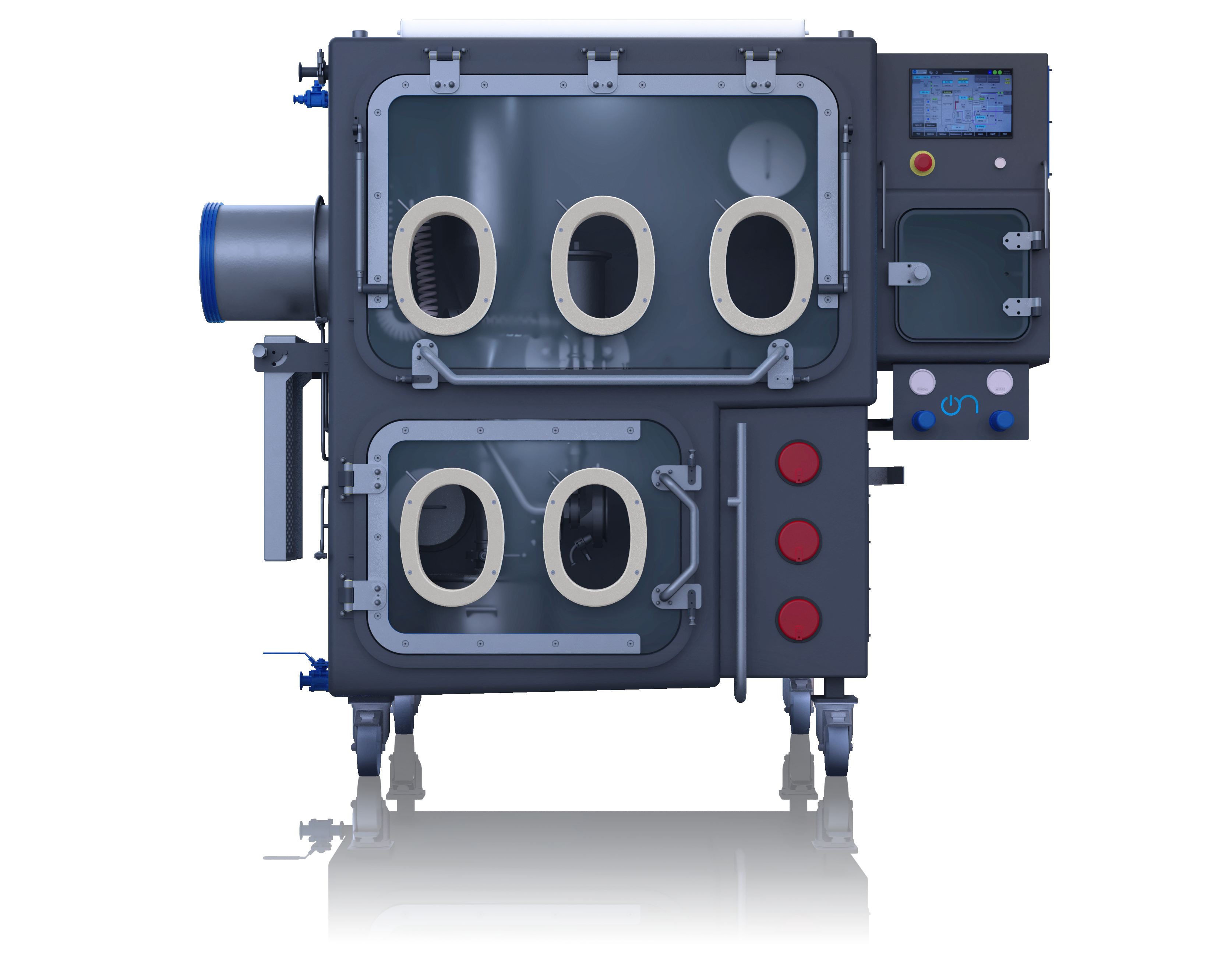
Isolators (Gloveboxes)
Isolators fulfill two important containment functions in the manufacturing process of battery materials. Firstly, they protect operators from the often toxic or carcinogenic raw and active materials. Secondly, they protect the products from contamination and thus increase product quality. Hosokawa ON provides isolators (gloveboxes) for these purposes that can be extended (additional glove-ports and sizes) depending on individual requirements and process workloads
Designed for manual and automated handling and processing, Hosokawa ON’s isolators are available in single and multi-cell variants for processes including milling, micronising, dispensing, sampling and product pack-off.
Applications
- Containment of hazardous products during battery production . Lithium battery materials include cathode materials, anode materials, conducive materials, graphene or nanomaterials etc.
- Product protection
- Safe and stable process conditions including inert oxygen and moisture free atmosphere, gas purification systems
- Integrate third party equipment (ovens, solvent purification systems)
Principle of operation
The isolator incorporates an extract system which maintains a negative pressure internally to ensure that any dust is contained inside the chamber and drawn into the extract filters.
Your advantages with an isolator
- Flexible isolator solutions (bespoke) for a high level of protection as well as easy cleaning, maintenance and disposal
- Window system (lift-up glass or acrylic), hinged and with an inflatable seal, for easy access to the equipment inside the glovebox
- Safe filter change options to limit the exposure of harmful products to the environment: Potentially hazardous material is captured in filters that can be exchanged safely
- Multi-chamber isolator for the highest level of containment:
- Example: upper isolator houses the fill head and the lower chamber houses the drum, customers obtain a dedicated extract and handling system with the option to clean the drum before disposal, ensuring optimal operator protection.
- Big bag discharge glovebox: big bags can be manually discharged in a glovebox to protect operators and the product.
- Glove Safe Change System: Gloves are safely exchanged without bringing the operator into contact with the product. The change operation is easy and quick without contamination of the product.
- Pass Box / Airlocks for complete isolation limiting exposure of the material to the environment
- Half Suit Isolators for improved operator access & ergonomics. The breathing air is filtered to protect the operators.
- Integrated engineering: Hosokawa powder processing equipment can be re-designed for installation inside Gloveboxes/isolators for a more bespoke processing response and delivering an improved ergonomic solution.
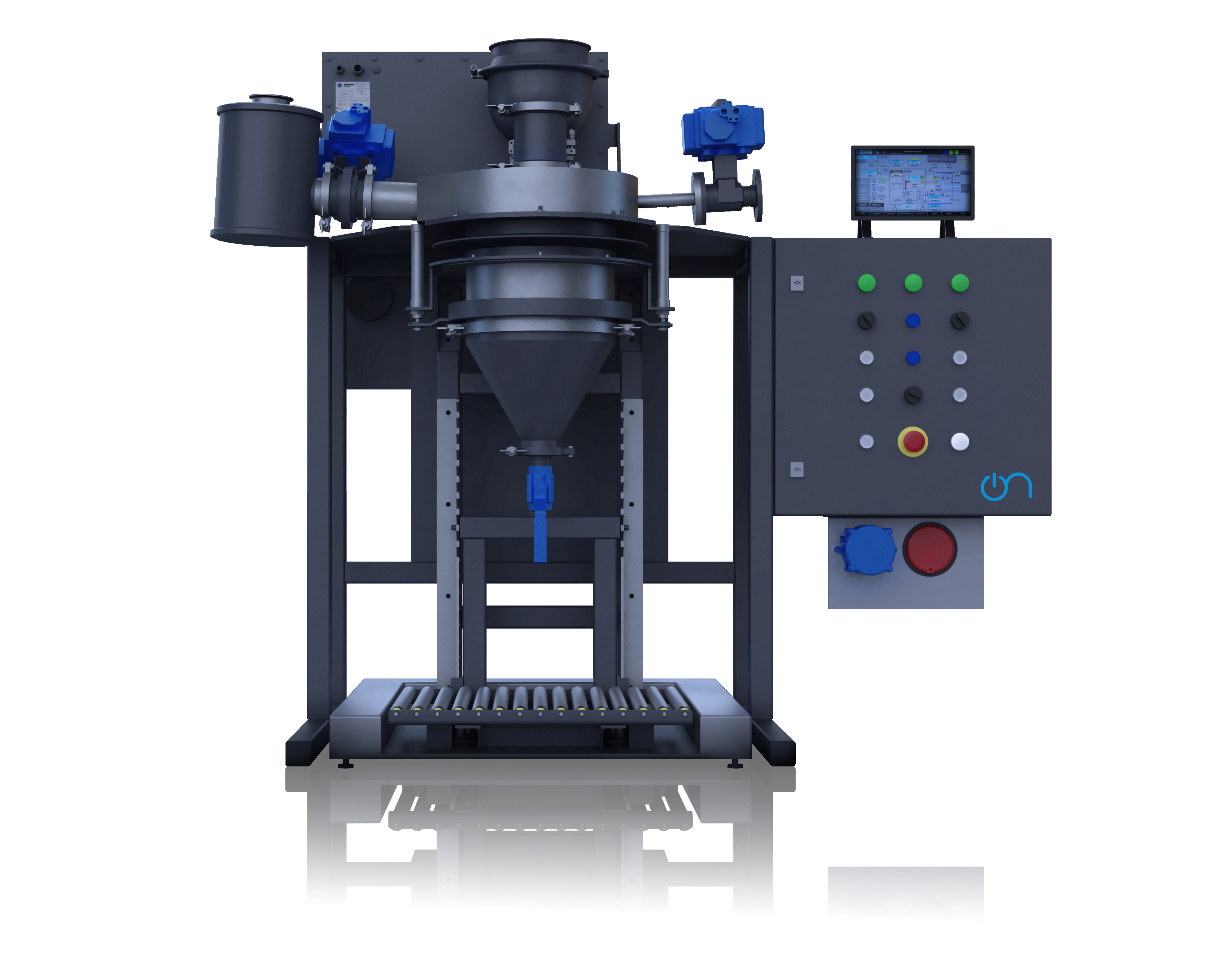
Filling & Weighing Systems
Filling and weighing are important process steps in the production of lithium-ion batteries. Our accurate weight-controlled filling systems maintain the highest standards of hygiene, dust control and product integrity. They deliver accurate, stable and repeatable weight readings and can be designed for use in hazardous areas. They incorporate interchangeable, Stott design inflatable packing heads and integrated weigh platforms to provide automatic control of bulk and dribble filling modes.
Applications
- Filling and weighing various raw and active materials in the production of lithium-ion batteries
Your advantages with our filling and weighing systems
- Our contained filling and weighing system is easy to operate and guarantees a high level of product integrity
- Designed for flexible filling of a range of containers of various sizes including drums with or without liners, IBC’s, FIBC’s, Polybottles, high containment flexible bags
- A single, easy to read, flush mounted control panel display, including continuous weight readout and other process parameters. The system can be connected to the customer’s distributed control system (DCS).
- Compact inward seal that does not come into contact with the product, or alternatively the fill weigh systems can be designed with outward inflatable seal or downward inflatable seal to suite the application.
- A range of dosing devices are available to achieve weighing accuracy during filling, ranging from simple butterfly valves to highly accurate screw feeders depending on material characteristics and accuracies required.
- Secondary containment is provided by enclosing the fill / weigh system inside one of Hosokawa’s Horizontal Laminar Flow Booths designed for the application or alternatively the filling system can be integrated into a Hosokawa Downflow booth or Hosokawa Glovebox/Isolator system.
- All of our systems are available in bespoke designs suitable to meet customers’ requirements for the application.
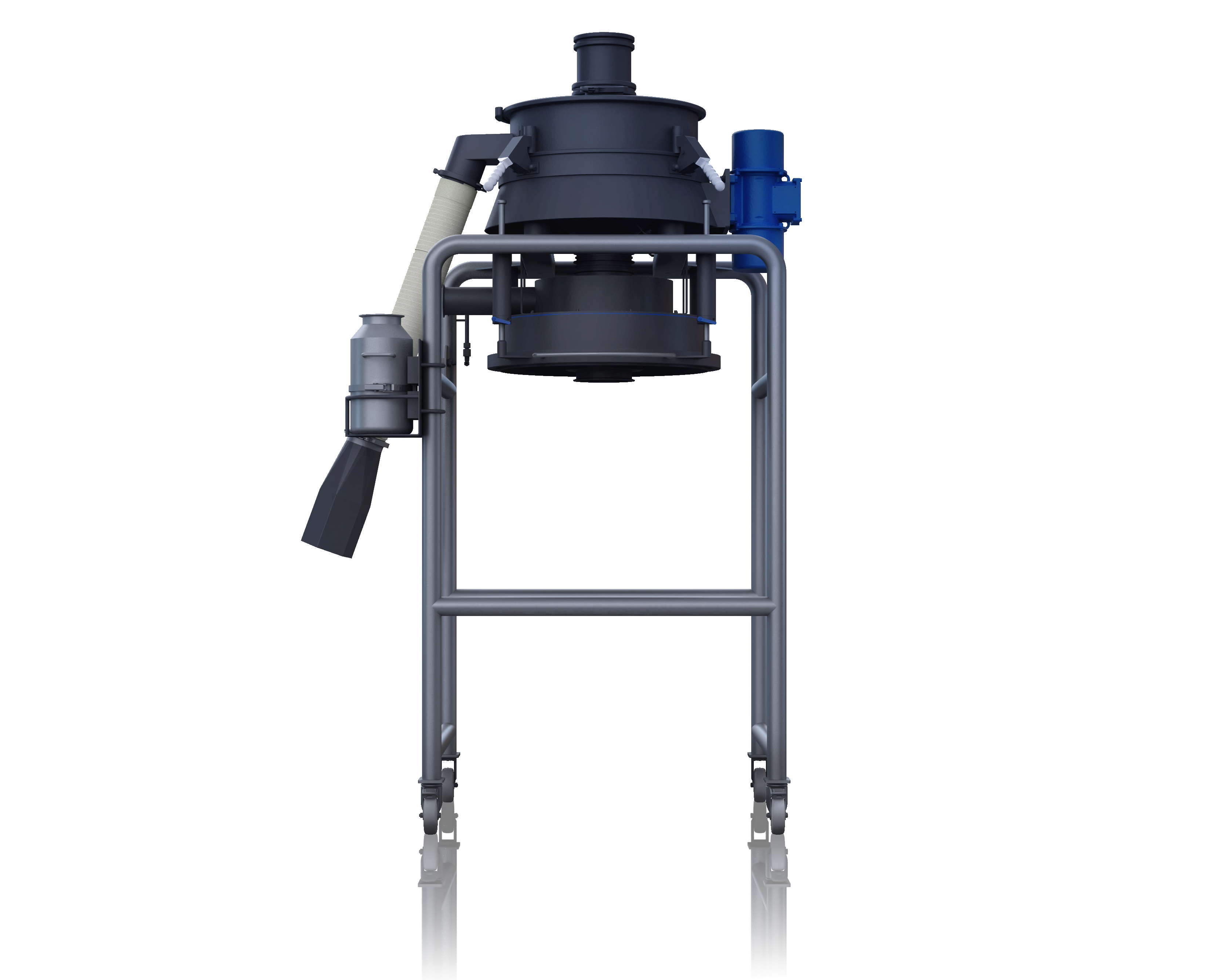
Packing Heads
Packing heads are an integral part of our filling and weighing systems and are used in various process steps in the production of lithium-ion batteries. On’s pack-off solutions are hardwearing, energy-efficient, easy to use and simple to maintain to make your battery production as efficient as possible.
Applications
- Packing of various raw and active materials in the production of lithium-ion batteries
Types of packing heads
Inward inflatable packing head seals the liner to the packing head on the outside of the liner sealing it onto the outside of the packing head and ensuring the seal does not come into contact with the product. There is no contact between the seal and the product meaning the seal stays clean and is easy to wipe clean. Quick product change overs as there is no contamination on the seal from previous products.
- Containment level is high.
- Product contact is none.
- Can be used with Single or Continuous liners
Outward inflatable packing head seals the liner to the packing head on the inside of the liner on the end of the packing chute, inflating like a tire. Only the very bottom of the natural rubber seal comes into contact with the product. There is minimal contact between the seal and the product meaning the seal stays largely clean and is easy to wipe clean. Product change overs require a quick wipe clean of the seal to ensure no residual contamination from previous products.
- Containment level is high.
- Product contact is minimal.
- Can be used with Single or Continuous liners
Downward sealing head – available in both inflatable and solid seal configurations. Typically used for sealing onto drums, intermediate bulk containers (IBC), bottles, the downward sealing head can be movable on cylinders or gas struts if required, to lower the head into the correct place to ensure correct containment of the container to be filled. Inflatable sealing heads provide even greater adjustment to ensure a perfect seal even with older, slightly damaged IBC’s.
- Containment level is high during filling.
- Containment level overall is medium as container is briefly open during changeover of containers to be filled.
- Can be used with drums both with and without liners.
O-ring canister packing head – simplest solution available, liner of drum or neck of FIBC sealed to the outside of the packing head by O-ring(s). O-ring provides seal during filling of the container/liner.
- Containment level is high.
- Product contact is minimal.
- Can be used with Single or Continuous liners
Your advantages with our packing heads
- Packing head system with single liners for a fast cycle time solution
- Packing head system with continuous liners prevents powder exposure to the local environment / operators.
- Packing head system with downward sealer for high volume discharge.
- Packing systems can come with combinations for filling FIBC/drum, IBC/drum and FIBC/IBC allows a flexible approach for diverse product duties.
- Safe change O-ring system limits or excludes powder exposure to the environment
- Packing head systems can be supplied with the following Hosokawa equipment for secondary or increased containment levels: Horizontal Laminar flow Booth, Downflow Booth or enclosed within one of our Glovebox/isolator systems for containment down to OEB5/6
- All our packing head systems can have built-in purge and exhaust of the filling head or be run under Air or an inert medium i.e. nitrogen purged. Built-in weighing system for real time weight display during filling possible as well as filling to a chosen set weight and vibration tables for powders that peak during filling
- Packing systems are available with ATEX, Control systems that can be stand-alone, PLC, integrated into Customer’s DCS site wide control systems, part of a SCADA system.
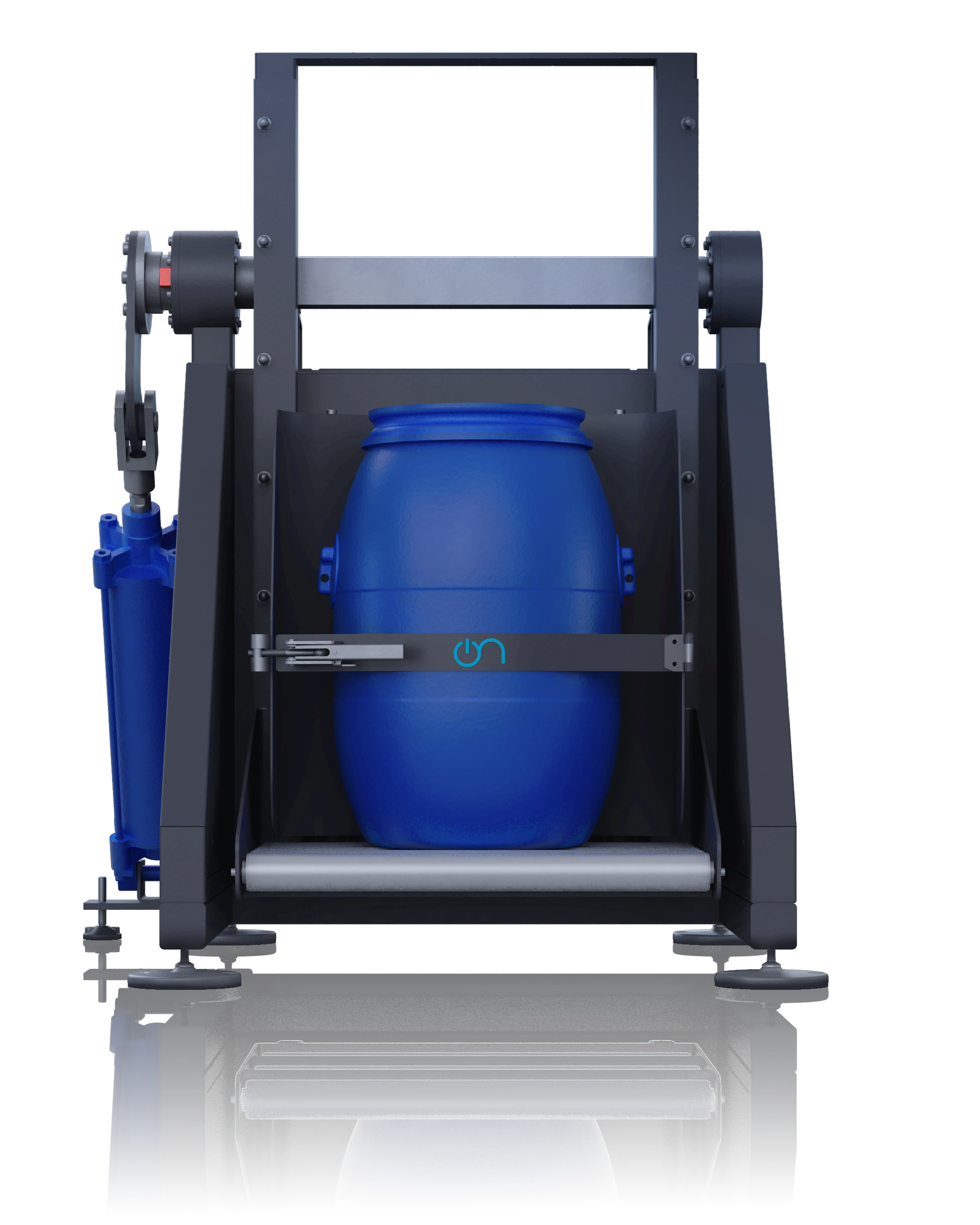
Drum Tippers
Drum handling equipment is used for safely introducing bulk raw material, including hazardous powder, into a process system, which may have a complex high containment element. Drum tippers are designed to minimise the amount of manual handling of the product
Applications
- Feeding raw and active cathode and anode materials into a process system
- Drums that contain hazardous substances pose several risks. Drums are often heavy and difficult to move while the contents may be harmful or even flammable. This means, under COSHH regulations, having the correct procedures and provisions for their handling are vital.
Principle of operation
Our drum tippers are tailored specifically for optimal performance and integration into our containment solutions, which can include everything from Downflow Booths, Gloveboxes and Isolators, to complex systems for the production of lithium-ion batteries.
Customizable drum tippers, manual or powered and ATEX certified models are available for customers’ specific needs.
Our automated drum tippers incorporate interlocked safety cages to ensure compliance to CE, UKCA and PUWER regulations, as well as multi-chamber isolators with integrated automatic drum tipping to meet maximum OEL requirements and provide complete product protection.
Your advantages with our drum tippers
- Glovebox with drum tipper: robust design at lower cost for containment and transfer of materials from drums into the glovebox
- Adherence to Good Manufacturing Practice (GMP)
- Electric, Pneumatic tippers, Hydraulic mechanical tippers available
- Tailor-made for integration into all Hosokawa Micron containment equipment
- ATEX rated versions available (Zone 1/21 and Zone 2/22)
- All of our solutions are supplied in stainless steel as standard, with a further option for powder-coated carbon steel, if required